Construction plywood stands as a testament to engineered wood’s remarkable strength and versatility in the realm of building and construction. This essential material, crafted from layers of cross-grained wood veneer, forms the backbone of countless structures, from towering skyscrapers to cozy homes. Its widespread use is a testament to its adaptability, affordability, and sheer strength. This comprehensive guide delves deep into the world of construction plywood, exploring its types, applications, advantages, limitations, and the factors to consider when choosing the perfect plywood for your construction project.
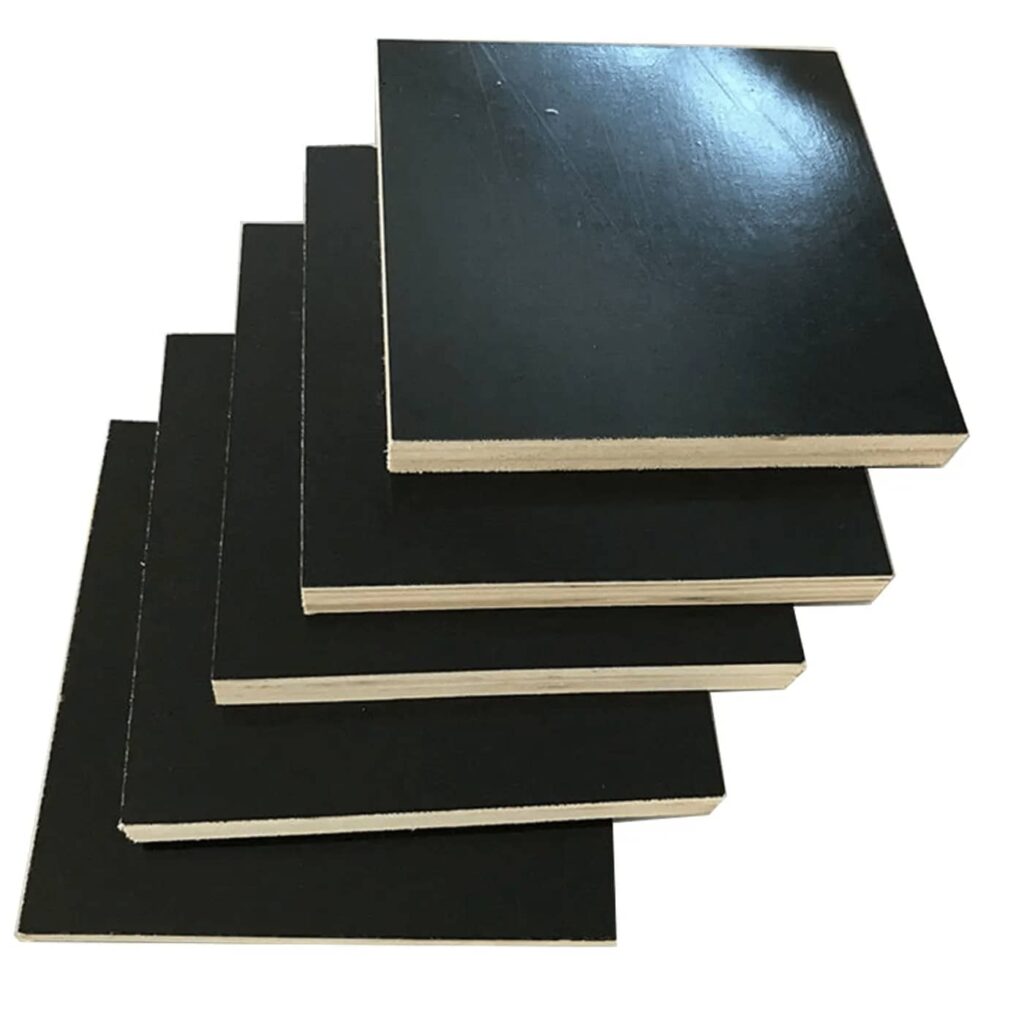
Deconstructing the Layers: Understanding Construction Plywood
Construction plywood distinguishes itself from other plywood types through its emphasis on structural integrity, durability, and affordability. While aesthetics might take a backseat, its ability to withstand heavy loads, resist moisture, and provide a stable substrate for various finishes makes it indispensable in construction. Imagine framing a house without the reliable strength of plywood sheathing, or erecting concrete walls without the smooth, reusable surface of formwork plywood. It’s the unsung hero of countless construction projects, silently providing the structural integrity and versatility that builders, from large construction firms to DIY enthusiasts, rely upon.
Key Characteristics of Construction Plywood:
- Structural Strength: Engineered with cross-grained layers, construction plywood exhibits exceptional strength and stiffness, capable of handling heavy loads and resisting bending and warping. This cross-graining, where each layer’s grain runs perpendicular to the adjacent layer, distributes the load across the entire sheet, making it far stronger than a single piece of wood of the same thickness. This makes it ideal for applications like wall sheathing, where it provides a robust backing for siding and helps transfer wind loads to the building’s foundation, ensuring the structure can withstand the elements.
- Moisture Resistance: While not entirely waterproof, construction plywood often incorporates moisture-resistant adhesives and treatments to withstand exposure to humidity and occasional dampness during construction. This is particularly important for exterior applications like roof decking, where it needs to resist moisture damage until the roofing material is installed, preventing warping and rot that could compromise the roof’s integrity.
- Dimensional Stability: The cross-grained construction minimizes expansion and contraction with changes in humidity, ensuring the plywood remains dimensionally stable over time. This stability is crucial for applications like subflooring, where it provides a level and consistent base for installing flooring materials, preventing squeaks and unevenness in the finished floor.
- Workability: Construction plywood can be easily cut, shaped, and fastened, making it a practical choice for various construction applications. Whether you’re using a circular saw, jigsaw, or nail gun, construction plywood’s workability speeds up construction and reduces labor costs, making it a favorite among contractors and builders working on tight deadlines.
- Cost-Effectiveness: Compared to solid lumber or other building materials, construction plywood offers an economical solution for large-scale projects or budget-conscious builds. Its large sheet size reduces the need for numerous smaller pieces, minimizing waste and installation time, which translates to cost savings in both material and labor.
Navigating the Types: Choosing the Right Construction Plywood
The world of construction plywood encompasses various types, each tailored to specific applications and environmental demands. Understanding these variations is crucial for selecting the right plywood for your project, ensuring its longevity and performance:
1. Sheathing Plywood:
The workhorse of construction plywood, sheathing plywood forms the structural skin of walls, roofs, and floors, providing a stable base for attaching siding, roofing materials, and flooring. It’s the unsung hero that provides strength, stability, and a nailing surface for subsequent layers in a building’s structure. Sheathing plywood is a staple for framers, roofers, and flooring installers, used in everything from single-family homes to large apartment complexes.
- Key Features:
- Focus on strength, stiffness, and affordability.
- Typically made with softwood veneers like Douglas fir or Southern Pine, known for their strength and availability.
- Graded based on exposure durability (Exposure 1, Exposure 2, Exterior), allowing you to choose the right level of moisture resistance for your project.
- Common Applications:
- Wall sheathing: Provides a structural nailing surface for siding, bracing, and insulation, creating a strong and rigid wall assembly that can withstand wind loads and impact. Used in residential and commercial buildings of all sizes.
- Roof decking: Forms a stable base for attaching shingles, tiles, or other roofing materials, transferring the weight of the roofing system to the roof trusses or rafters. Essential for distributing roof loads to the building’s framing and preventing sagging.
- Subflooring: Creates a smooth and level surface for installing various flooring materials, including hardwood, tile, and carpet, providing a stable base that prevents movement and squeaking in the finished floor.
2. Structural Plywood:
Engineered for demanding load-bearing applications, structural plywood boasts superior strength and stiffness compared to sheathing plywood. It’s the go-to choice when the plywood itself needs to carry significant weight or resist bending forces, making it essential for structural components in buildings of all sizes. Structural plywood is often specified by engineers and architects for projects requiring specific load-bearing capacities.
- Key Features:
- Manufactured with higher-grade veneers and stronger adhesives, resulting in a denser and more robust panel capable of handling heavier loads.
- Often meets specific building code requirements for structural applications, ensuring it complies with safety standards and regulations.
- Common Applications:
- Beams: Used in conjunction with lumber to create strong and rigid beams that support floors, roofs, and other structural elements, spanning larger distances and carrying heavier loads than lumber alone.
- Headers: Span openings in walls, such as doors and windows, transferring loads to the surrounding framing, preventing the wall from sagging or collapsing above the opening.
- Floor joists: Provides a cost-effective alternative to solid lumber joists in certain applications, especially in manufactured homes, offering comparable strength and stiffness at a lower price point.
- Wall bracing: Enhances the structural stability of walls, resisting racking forces from wind and seismic activity, preventing the walls from twisting or collapsing under lateral loads.
3. Fire-Resistant Plywood:
This specialized type undergoes treatment with fire-retardant chemicals to slow the spread of flames and smoke, meeting stringent fire codes in commercial and residential buildings. It’s a crucial component in fire-rated assemblies, helping to contain fires and provide valuable time for evacuation, potentially saving lives and property. Fire-resistant plywood is essential for any project where fire safety is a paramount concern, including schools, hospitals, and multi-family dwellings.
- Key Features:
- Meets specific fire-resistance ratings based on testing and building codes, ensuring it meets the required level of fire protection for its intended application.
- Often required for walls, ceilings, and other structural components in fire-rated assemblies, preventing the spread of fire and smoke between rooms, floors, or buildings.
- Common Applications:
- Apartment buildings: Used in fire-rated walls and ceilings to separate units and limit fire spread, protecting occupants and containing fires to their origin.
- Commercial structures: Essential for fire-rated partitions, elevator shafts, and other areas requiring fire containment, protecting occupants and limiting property damage in the event of a fire.
- Fire-rated walls and ceilings: Used in any building where fire codes mandate fire-resistant construction, providing a critical layer of protection against the spread of fire.
4. Marine Plywood:
While not strictly classified as “construction” plywood, marine plywood’s exceptional moisture resistance makes it suitable for specific construction applications in high-humidity environments. It’s the go-to choice when plywood will be exposed to prolonged moisture or high humidity, preventing rot, delamination, and structural degradation. Marine plywood is favored by boat builders, dock builders, and anyone constructing structures exposed to water or high humidity.
- Key Features:
- Utilizes waterproof adhesives to prevent delamination and rot, ensuring the layers of veneer remain bonded even in wet conditions.
- Made with durable wood species like Douglas fir or Western Larch, known for their natural resistance to decay and moisture damage.
- Features a void-free core for enhanced water resistance, preventing water from seeping into the plywood’s core and causing internal rot.
- Common Applications:
- Exterior siding in humid climates: Provides a durable and moisture-resistant alternative to traditional wood siding in areas with high rainfall or humidity, preventing rot and maintaining its structural integrity.
- Soffits and fascia: Resists moisture damage in these exposed areas of a roof’s overhang, preventing rot and maintaining the aesthetic appeal of the roofline.
- Bathroom subfloors and walls: Withstands the high moisture levels present in bathrooms, preventing rot and mold growth, ensuring the longevity of the bathroom structure.
5. Sanded Plywood:
While primarily used for furniture and cabinetry, sanded plywood’s smooth surface can be suitable for certain construction applications where a finished appearance is desired. It offers a step up from rough construction plywood when a smoother surface is needed for painting or finishing, providing a more refined look for interior applications. Sanded plywood is often used by finish carpenters, cabinetmakers, and DIY enthusiasts looking for a smooth, paintable surface.
- Key Features:
- Features a sanded face veneer for a smooth, ready-to-finish surface, eliminating the need for extensive sanding before painting or finishing.
- Available in various wood species and grades, allowing you to choose the right combination of appearance and affordability for your project.
- Common Applications:
- Wall paneling: Creates a warm and inviting look in residential and commercial spaces, adding a touch of elegance and sophistication to interior walls.
- Ceiling liners: Provides a smooth and finished surface for ceilings, concealing ductwork and other utilities while enhancing the aesthetic appeal of the space.
- Built-in shelving units: Offers a durable and aesthetically pleasing material for custom shelving solutions, providing a smooth and attractive surface for displaying books, decorations, or other items.
Decoding the Grades: Understanding Plywood Quality Standards
Construction plywood is graded based on the quality of its face and back veneers, influencing its appearance, durability, and suitability for specific applications. Understanding these grades is essential for choosing plywood that meets both structural and aesthetic requirements, ensuring you get the right balance of performance and appearance for your project.
Grade | Description | Typical Applications |
---|---|---|
A | Smooth, paintable surface with minimal imperfections. Suitable for natural finishes or painting. | Cabinetry, furniture, high-end wall paneling. This grade is typically used where the plywood surface will be visible and requires a high-quality finish, free from knots, voids, or other blemishes that could detract from the final appearance. |
B | Solid surface with a few minor imperfections. Suitable for painting or covering with other materials. | Wall sheathing, roof decking, subflooring. This grade balances quality and affordability, making it suitable for applications where the plywood will be covered by other materials, such as siding, roofing, or flooring, hiding minor imperfections. |
C | May have knotholes and other imperfections. Suitable for applications where appearance is not a primary concern. | Concrete formwork, temporary structures, packaging. This grade prioritizes affordability over appearance and is suitable for applications where the plywood’s appearance is not a factor, such as concrete forms that will be removed after the concrete cures. |
D | Lowest grade with significant imperfections. Typically used for structural applications where appearance is not a factor. | Sheathing under siding, backing for cabinets, industrial applications. This grade is the most economical option and is suitable for applications where the plywood will be hidden from view, providing structural support without the need for a finished appearance. |
X | Denotes exterior glue. Can be combined with other letter grades (e.g., CDX) to indicate the glue type and veneer quality. | Exterior sheathing, roof decking, applications exposed to moisture. This designation ensures the plywood can withstand exposure to the elements without delaminating or deteriorating, maintaining its structural integrity in demanding conditions. |
Note: Plywood grades are often combined to denote the quality of both the face and back veneers (e.g., AB, CDX). For example, CDX plywood has a C-grade face veneer, a D-grade back veneer, and is bonded with exterior glue, making it suitable for exterior sheathing applications where the rough C-grade face will be covered by siding.
Making the Right Choice: Factors to Consider
Selecting the right construction plywood requires careful consideration of your project’s specific requirements, ensuring you choose a material that meets both the structural demands and the aesthetic goals of your build:
- Application: The intended use dictates the plywood type, grade, and thickness. Structural applications, like floor joists, demand higher-grade plywood with greater strength and stiffness than sheathing or subflooring. Consider the load-bearing requirements, moisture exposure, and fire resistance needs of your project, consulting building codes and span tables to determine the appropriate plywood for your specific application.
- Load-Bearing Requirements: Consult building codes and span tables to determine the appropriate plywood thickness and grade for load-bearing applications like floors, roofs, and walls. These tables provide guidelines for maximum spans based on plywood thickness, grade, and support spacing, ensuring your structure meets safety standards and can handle the anticipated loads.
- Moisture Exposure: Assess the environment where the plywood will be used. For exterior applications or areas prone to moisture, opt for exterior-grade plywood with waterproof adhesives, preventing delamination and rot. Consider marine plywood for extreme conditions, such as boat building or applications with prolonged water exposure, where maximum moisture resistance is crucial.
- Fire Resistance: If fire safety is a concern, choose fire-resistant plywood that meets the required fire codes and regulations. This is especially important for multi-family dwellings, commercial buildings, and other structures where fire safety is paramount, helping to contain fires and provide valuable time for evacuation.
- Budget: Plywood prices vary depending on type, thickness, and grade. Balance your budget constraints with the required performance characteristics, choosing the most cost-effective option that still meets the structural and aesthetic demands of your project. While it’s tempting to choose the most affordable option, investing in higher-quality plywood for critical applications can save on costly repairs or replacements down the line.
Working with Construction Plywood: Tips for Success
While construction plywood is generally easy to work with, following these tips can enhance your results and ensure a successful project, whether you’re a seasoned contractor or a DIY enthusiast:
- Cutting: Use a sharp saw blade specifically designed for plywood to prevent chipping and splintering, ensuring clean and accurate cuts. Carbide-tipped blades with a high tooth count are ideal for smooth cuts, minimizing tear-out and splintering, especially on the face veneer. Score the cut line with a utility knife to further reduce chipping, creating a cleaner edge and preventing the veneer from splintering.
- Drilling: Predrill holes, especially near edges, to prevent splitting, allowing the screw to penetrate smoothly without putting excessive pressure on the surrounding wood fibers. Use a drill bit slightly larger than the screw shank to allow for wood movement and prevent the screw from binding, preventing the plywood from cracking or splitting as it expands and contracts with changes in humidity. Countersink screw heads for a flush finish, creating a smooth surface for subsequent finishing steps.
- Fastening: Choose screws or nails appropriate for the plywood thickness and the application, ensuring the fasteners have sufficient holding power and won’t protrude through the other side of the plywood. Space fasteners evenly and use construction adhesive for added strength and stability, creating a stronger bond between the plywood and the framing members. Consult fastener charts for recommended spacing and penetration depths, ensuring the fasteners provide adequate holding power without compromising the plywood’s structural integrity.
- Moisture Protection: Seal all edges and cut ends of plywood with a sealant or primer to prevent moisture absorption, especially in exterior applications. This helps prevent swelling, warping, and rot, extending the life of the plywood and maintaining its structural integrity. Use a paintable sealant if the plywood will be painted, creating a suitable surface for paint adhesion and preventing moisture from penetrating the plywood through the paint layer.
Conclusion: Building a Solid Foundation
Construction plywood, with its exceptional strength, versatility, and affordability, plays a vital role in shaping the world’s buildings. From humble homes to towering skyscrapers, it provides the structural backbone that supports our built environment, offering a reliable and cost-effective solution for countless construction needs. By understanding the different types, grades, and applications of construction plywood, you can confidently choose the right material for your project, ensuring a solid foundation for years to come.