Engineered veneer LVL (Laminated Veneer Lumber) slats represent a triumph of modern engineering, offering a construction material that surpasses traditional lumber in strength, consistency, and versatility. These remarkable building blocks, crafted from layers of engineered veneer, are revolutionizing the way we build, offering superior performance and sustainability. This deep dive explores the intricacies of engineered veneer LVL slats, focusing on the pivotal role of engineered veneer in their creation, their diverse applications, and the compelling reasons why they are becoming the material of choice for discerning builders and architects.
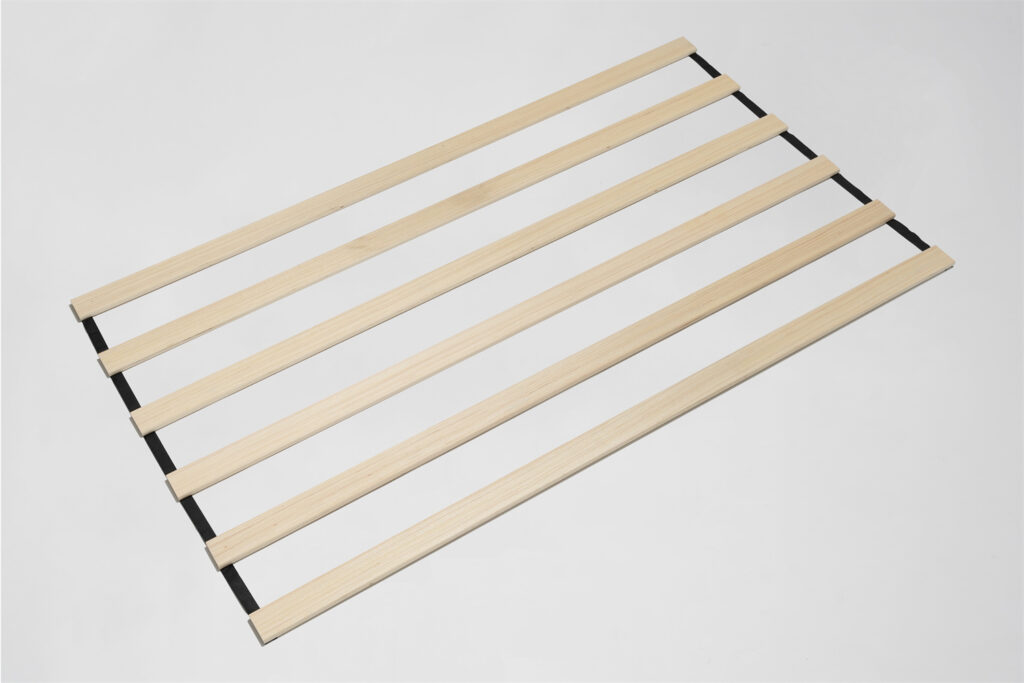
The Essence of Engineered Veneer: A Foundation of Strength
At the heart of every engineered veneer LVL slat lies the remarkable strength and stability of engineered veneer. This engineered wood product, created by bonding thin sheets of wood veneer together with their grain running parallel, forms the foundation for LVL’s exceptional properties.
Let’s delve into the key aspects of engineered veneer that make it such a game-changer in the world of construction materials:
- Veneer Selection and Preparation: The journey of engineered veneer begins with the careful selection of high-quality logs, typically from fast-growing, sustainable tree species like Douglas fir or Southern Pine. These logs are then peeled into thin sheets of veneer, ranging from 1/8″ to 3/16″ thick, using specialized rotary lathes. The veneer sheets are then dried to a specific moisture content, typically around 10-12%, to ensure dimensional stability and prevent warping or twisting during the LVL manufacturing process.
- Grain Orientation: The Key to Strength: The defining characteristic of engineered veneer lies in the parallel orientation of the wood grain in each layer. This deliberate alignment, unlike the random grain orientation found in solid lumber, maximizes the wood’s natural tensile strength, resulting in a product that’s significantly stronger and stiffer than solid lumber of comparable dimensions. This predictable strength and stiffness make engineered veneer ideal for structural applications where consistent performance is paramount.
- Adhesive Technology: Bonding for Performance: Engineered veneer layers are bonded together using strong, moisture-resistant adhesives, typically phenol-formaldehyde or melamine-formaldehyde resins. These adhesives play a critical role in transferring loads between the veneer layers, ensuring the structural integrity of the final LVL slat. Advances in adhesive technology have led to the development of even stronger and more moisture-resistant bonds, further enhancing the performance and longevity of LVL products, even in demanding environmental conditions.
- Advantages of Engineered Veneer: The use of engineered veneer in LVL slats offers a multitude of advantages:
- Enhanced Strength and Stiffness: The parallel grain orientation and strong adhesive bonds result in LVL slats with exceptional strength-to-weight ratios, surpassing those of traditional lumber. This allows for longer spans, reduced need for intermediate supports, and the ability to carry heavier loads, ultimately leading to more efficient and cost-effective designs.
- Dimensional Stability: Engineered veneer’s inherent resistance to warping, twisting, and shrinking translates into LVL slats with exceptional dimensional stability. This means they are less likely to change shape or size due to fluctuations in temperature and humidity, ensuring structural integrity and minimizing callbacks related to wood movement over time.
- Consistent Quality: The manufacturing process of engineered veneer allows for greater control over quality and consistency compared to traditional lumber, which can have significant variations in strength and appearance. Each sheet of veneer is inspected and graded, ensuring that only the highest quality materials are used in LVL production. This results in a more predictable and reliable building material.
- Efficient Use of Resources: Engineered veneer production allows for the use of smaller diameter logs and lower-grade veneers that might not be suitable for traditional lumber. This maximizes the use of harvested timber, making LVL slats a more sustainable building material that reduces reliance on old-growth forests.
Engineered Veneer LVL Slats: Applications Across Industries
The remarkable properties of engineered veneer LVL slats have made them indispensable in a wide range of applications, spanning construction, transportation, furniture making, and more. Their strength, stability, and versatility make them a go-to choice for builders, architects, and designers seeking high-performance building materials.
1. Construction and Building: This is where engineered veneer LVL slats truly shine, offering exceptional performance in a wide range of structural applications.
- Floor Joists and Rafters: LVL slats are widely used as floor joists and rafters in residential and commercial construction, favored by builders for their strength and ability to span greater distances. Their high strength-to-weight ratio allows for longer spans, reducing the need for intermediate supports and creating more open, flexible floor plans. This translates to fewer columns obstructing living spaces and greater design freedom for architects.
- Headers and Beams: LVL slats excel in creating strong and stable headers and beams that support roof loads and openings in walls. Their ability to span large openings without sagging or deflecting makes them essential for structural integrity, especially in modern homes with open-concept designs and large window expanses.
- Rim Boards and Wall Plates: LVL slats provide a strong and stable base for walls and roofs, ensuring even load distribution and structural integrity. They are particularly valuable in areas prone to high winds or seismic activity, where a robust structural framework is crucial.
- Scaffolding Planks: The strength and stiffness of LVL slats make them suitable for use as scaffolding planks, providing a safe and stable platform for workers at elevated heights. Their consistent dimensions and resistance to warping ensure a level working surface, enhancing safety on construction sites.
2. Transportation and Material Handling: The durability and moisture resistance of engineered veneer LVL slats make them ideal for transportation applications where exposure to the elements is a concern.
- Pallet Slats: LVL slats are commonly used in the construction of pallets due to their strength, durability, and resistance to moisture. They provide a reliable base for stacking, storing, and transporting goods, ensuring that products arrive at their destination undamaged. Their consistent dimensions also contribute to efficient stacking and storage.
- Shipping Crates: For heavy-duty shipping crates that need to withstand the rigors of transportation, LVL slats offer the necessary strength and dimensional stability to protect valuable goods. They are often used for shipping sensitive equipment, machinery, and other high-value items that require robust protection during transit.
3. Furniture Making: Beyond their structural capabilities, engineered veneer LVL slats have found their way into furniture making, where their strength and stability are highly valued.
- Tabletops and Shelving: LVL slats can be used to create strong and stable tabletops and shelving units, ensuring a flat and level surface even under heavy loads. Their resistance to warping and sagging makes them ideal for furniture pieces that need to withstand years of use.
- Furniture Frames: The dimensional stability and strength of LVL slats make them suitable for constructing durable furniture frames for chairs, sofas, and beds. Their ability to hold fasteners well and resist racking (distortion under load) ensures that furniture pieces remain sturdy and reliable over time.
4. Other Applications: The versatility of engineered veneer LVL slats extends to a variety of other applications, highlighting their adaptability and performance benefits.
- Bridge Decking: LVL slats are used in bridge construction for their strength, stiffness, and durability, providing a stable and long-lasting surface for vehicular and pedestrian traffic. Their ability to withstand heavy loads and resist weathering makes them a reliable choice for bridge infrastructure.
- Sign Posts and Supports: The resistance to weathering and decay makes LVL slats a suitable choice for sign posts and supports, ensuring visibility and longevity. Their strength and dimensional stability ensure that signs remain upright and securely in place, even in challenging weather conditions.
Factors Influencing the Performance of Engineered Veneer LVL Slats
While the manufacturing process ensures a high level of quality and consistency, several factors can influence the performance of engineered veneer LVL slats:
- Veneer Quality: The quality of the wood veneer used directly impacts the strength and stiffness of the final LVL slat. Higher-grade veneers, free from defects like knots and splits, result in stronger and more stable LVL products. Veneer quality is influenced by factors such as the species of wood, the growth conditions of the tree, and the care taken during harvesting and processing.
- Adhesive Type and Application: The type of adhesive used and its application method play a crucial role in the bond strength and moisture resistance of LVL slats. The adhesive must be compatible with the wood species used and applied evenly across the veneer surfaces to ensure a strong and durable bond. The curing process, which involves heat and pressure, is also critical in achieving optimal bond strength.
- Manufacturing Process: The precision and control of the manufacturing process, including veneer layering, pressing, and curing, directly impact the quality and consistency of the final product. Advanced manufacturing techniques, such as continuous pressing and radio-frequency curing, contribute to the production of high-performance LVL slats with uniform properties.
- Environmental Conditions: While engineered veneer LVL slats offer good moisture resistance thanks to the use of moisture-resistant adhesives and the inherent stability of engineered veneer, prolonged exposure to extreme humidity or wet conditions can still affect their performance. Proper sealing and protection are essential, especially in exterior applications or areas with high humidity levels, to prevent moisture absorption and potential issues like swelling or delamination.
Frequently Asked Questions about Engineered Veneer LVL Slats
1. How do engineered veneer LVL slats compare to traditional solid lumber in terms of cost?
While the initial cost of engineered veneer LVL slats is typically higher than that of comparable dimensional lumber, the overall cost-effectiveness of LVL often proves superior. Their increased strength and span capabilities can lead to material savings, as fewer LVL slats are needed to achieve the same structural support. Additionally, the dimensional stability of LVL reduces the likelihood of costly callbacks due to warping or twisting, further contributing to long-term cost savings.
2. Can engineered veneer LVL slats be used in exterior applications where they will be exposed to moisture?
Yes, engineered veneer LVL slats can be used in exterior applications, but proper precautions must be taken to protect them from moisture. While the manufacturing process incorporates moisture-resistant adhesives, prolonged exposure to wet conditions can still lead to performance issues. It’s crucial to choose LVL slats specifically treated for exterior use and to apply appropriate sealants or coatings to further enhance their moisture resistance.
3. Are engineered veneer LVL slats fire-resistant?
Engineered veneer LVL slats, like all wood products, are combustible. However, their inherent strength and predictable charring rate make them suitable for use in fire-rated assemblies when designed and detailed according to building codes. Fire-retardant treatments can also be applied to LVL slats to enhance their fire resistance.
4. Can engineered veneer LVL slats be cut and shaped on-site like traditional lumber?
Yes, engineered veneer LVL slats can be cut to size and shaped on-site using standard woodworking tools. However, it’s essential to follow the manufacturer’s recommendations for cutting and drilling to avoid compromising the structural integrity of the slats.
5. What is the lifespan of engineered veneer LVL slats?
Engineered veneer LVL slats, when properly installed and maintained, can last for decades. Their durability, strength, and resistance to warping and shrinking contribute to their long lifespan, making them a reliable and long-lasting building material.
Conclusion: Engineered Veneer LVL Slats – A Testament to Innovation
Engineered veneer LVL slats embody the spirit of innovation in the construction industry, offering a superior alternative to traditional lumber in terms of strength, stability, versatility, and sustainability. As we strive to build more durable, efficient, and environmentally responsible structures, engineered veneer LVL slats will undoubtedly play an increasingly vital role in shaping the future of building. Their ability to meet the demands of modern construction, coupled with their sustainable attributes, makes them a compelling choice for builders, architects, and anyone seeking to build a better future.