2The construction world thrives on choices – materials, techniques, styles – each decision shaping the final masterpiece. Among these pivotal choices lies the selection of sheet materials, the unsung heroes providing structure and support to countless projects. And in this arena, two titans often clash: Plywood vs MDF. Both versatile, both popular, but each possessing unique strengths and weaknesses.
This head-to-head comparison transcends a simple “which is better” debate. It’s about empowering you, the discerning builder, architect, or designer, to confidently choose the material that aligns perfectly with your project’s demands, budget, and desired outcome.
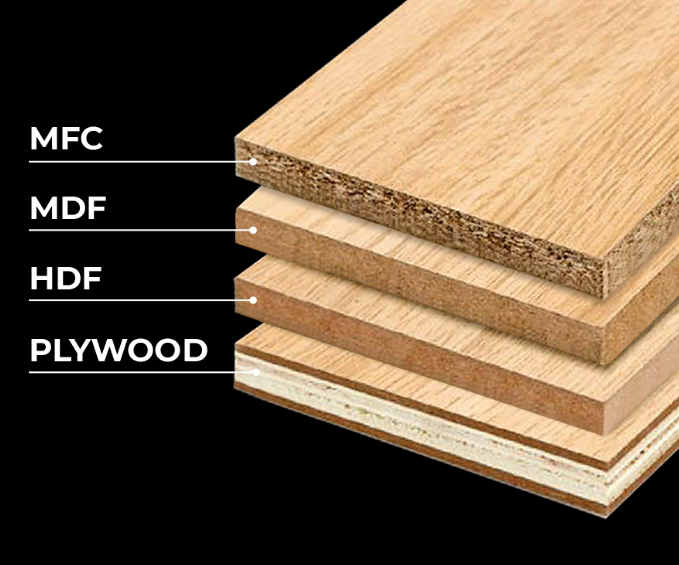
Understanding the Contenders: A Tale of Two Materials
Before diving into the ringside analysis, let’s get acquainted with our contenders:
1. Plywood: The Layered Champion
Imagine thin sheets of wood veneer, meticulously layered with alternating grain directions, and bonded together under intense pressure and heat. That’s plywood – a symphony of strength derived from its cross-grained structure.
Key Characteristics:
- Strength: The cross-graining provides exceptional strength and dimensional stability, resisting warping, bending, and twisting.
- Versatility: Available in various wood species, thicknesses, and grades, catering to diverse applications, from structural framing to fine furniture.
- Moisture Resistance: Certain types, like marine plywood, are specifically treated for enhanced moisture resistance, making them suitable for exterior applications or humid environments.
2. MDF: The Smooth Operator
MDF, or Medium-Density Fiberboard, takes a different approach. Imagine fine wood fibers, almost like sawdust but more refined, mixed with resin and pressed into smooth, uniform panels.
Key Characteristics:
- Smooth Surface: Ideal for painting or veneering, offering a consistent, void-free surface that requires minimal preparation.
- Affordability: Often more budget-friendly than plywood, especially for large-scale projects or applications where cost is a primary concern.
- Consistency: Its uniform composition ensures consistent density and performance throughout the panel, minimizing variations or imperfections.
Round 1: Strength and Durability – Where Plywood Flexes Its Muscles
When it comes to sheer brawn, plywood emerges as the undisputed champion. Its cross-grained structure gives it exceptional strength-to-weight ratio, making it ideal for applications where load-bearing capacity and structural integrity are paramount. This is why plywood is the go-to choice for contractors, builders, and DIY enthusiasts engaged in projects demanding robust structural support.
Plywood’s Advantages:
- Superior Strength: Holds fasteners (screws, nails) exceptionally well, crucial for structural framing, subfloors, or heavy-duty shelving. This makes it a favorite for framing walls, constructing roofs, and building sturdy floors that can withstand years of use.
- Impact Resistance: Withstands impacts and shocks better than MDF, making it suitable for high-traffic areas or applications prone to accidental bumps. Think bustling hallways, busy kitchens, or workshops where tools might be dropped.
- Moisture Resistance: While standard plywood is susceptible to moisture damage, treated varieties like marine plywood excel in humid environments. This makes them the preferred choice for boat builders, outdoor furniture makers, and projects in coastal regions.
MDF’s Limitations:
- Lower Strength: Not as strong as plywood, especially when spanning large distances or supporting heavy loads. This makes it less suitable for structural applications where significant weight-bearing capacity is required.
- Fastener Holding: While it holds screws adequately, its dense, compressed structure may lead to screw blowouts if not handled carefully. This requires extra care during installation to prevent damage to the material.
- Moisture Vulnerability: Standard MDF is highly susceptible to swelling, warping, or crumbling when exposed to moisture, limiting its use in humid or exterior applications. This makes it unsuitable for outdoor projects or areas with high moisture levels, like bathrooms, unless specifically treated.
Winner: Plywood
Round 2: Smoothness and Finish – MDF’s Time to Shine
While plywood boasts strength, MDF counters with its impeccable smoothness and finish. Its uniform composition creates a pristine canvas, ideal for projects demanding a flawless painted or veneered surface. This characteristic makes MDF a favorite among cabinet makers, furniture designers, and craftspeople who value a refined, polished look.
MDF’s Advantages:
- Ultra-Smooth Surface: Requires minimal sanding, saving time and labor costs during finishing. This is a significant advantage for projects where a pristine surface is paramount, such as painting cabinet doors or creating smooth furniture components.
- Consistent Density: Ensures a uniform finish, free from grain patterns or voids that might telegraph through paint or veneer. This consistency is especially valuable when applying thin veneers or achieving a flawless paint job.
- Takes Paint Beautifully: Provides an excellent base for paint, resulting in a smooth, professional-looking finish. This makes it ideal for projects where a painted finish is desired, such as interior doors, moldings, or decorative elements.
Plywood’s Limitations:
- Visible Grain Pattern: The wood veneer surface, while aesthetically pleasing in some applications, may require extensive sanding or filling to achieve a perfectly smooth painted finish. This can add time and cost to the finishing process.
- Potential for Telegraphed Grain: Changes in temperature or humidity can cause slight wood movement, potentially leading to visible grain patterns “telegraphing” through paint over time. This is less of a concern for applications where the wood grain is desired or where a more rustic aesthetic is acceptable.
Winner: MDF
Round 3: Versatility and Applications – A Close Call
Both plywood and MDF are versatile materials, but their strengths dictate their ideal applications. Plywood, with its strength and structural integrity, finds its home in applications demanding robust support and durability. MDF, on the other hand, shines in projects where a smooth, consistent finish is paramount, making it a favorite for cabinetry, furniture, and decorative elements.
Plywood’s Domain:
- Structural Framing: Walls, roofs, floors – where strength and stability are non-negotiable. This is the backbone of countless construction projects, providing the essential framework for homes, buildings, and structures of all kinds.
- Subfloors: Provides a stable base for various flooring materials, from hardwood to tile. Its strength and dimensional stability ensure a level, long-lasting foundation for your chosen flooring.
- Sheathing: Exterior walls, roofs – offering structural support and a nailing surface for siding, roofing materials. This acts as a protective layer, providing strength and a base for attaching exterior finishes.
- Heavy-Duty Furniture: Shelving units, workbenches, furniture designed for heavy loads or frequent use. Plywood’s strength ensures these pieces can withstand the rigors of daily use without compromising their structural integrity.
- Exterior Applications: Marine plywood, with its enhanced moisture resistance, is ideal for boat building, outdoor furniture, or exterior siding. This specialized plywood is engineered to withstand the challenges of moisture, humidity, and exposure to the elements.
MDF’s Niche:
- Cabinetry: Offers a smooth, consistent surface for cabinet doors, drawer fronts, and cabinet boxes. Its ability to accept paint and veneer beautifully makes it a top choice for achieving a polished, professional look in kitchens, bathrooms, and throughout the home.
- Furniture: Suitable for lighter-duty furniture pieces, especially those with painted or veneered surfaces. MDF provides a cost-effective and aesthetically pleasing option for creating furniture with a modern, sleek appearance.
- Molding and Trim: Its smooth, consistent profile makes it ideal for creating decorative moldings, trim work, or architectural details. MDF can be easily shaped and cut to create intricate designs, adding a touch of elegance and sophistication to any space.
- Signboards and Displays: Provides a smooth, stable surface for painting, printing, or mounting graphics. Its consistent density ensures a uniform finish, making it ideal for creating eye-catching signs, displays, and promotional materials.
Winner: It’s a tie! Both materials excel in their respective domains.
Round 4: Cost Comparison – MDF Takes the Lead
Cost is often a deciding factor in construction projects, and here, MDF generally holds the advantage. Its affordability makes it an attractive option for budget-conscious builders, while plywood’s higher cost is often justified by its superior strength and durability.
MDF’s Affordability:
- Lower Material Costs: The manufacturing process and readily available raw materials make MDF generally more budget-friendly than plywood. This cost advantage can be significant, especially for large-scale projects where material costs make up a considerable portion of the budget.
- Potential Labor Savings: Its smooth surface requires less preparation time for finishing, potentially reducing labor costs. This can further enhance its cost-effectiveness, as less time is spent on sanding, priming, and preparing the surface for paint or veneer.
Plywood’s Cost Considerations:
- Higher Upfront Cost: Plywood, especially higher grades or specialty types like marine plywood, can be significantly more expensive than MDF. This higher cost reflects the superior quality, strength, and moisture resistance of these plywood varieties.
- Potential Labor Costs: Achieving a perfectly smooth finish on plywood may require additional sanding or filling, increasing labor time and costs. This is especially true if a flawless painted finish is desired, as the wood grain may require extra preparation.
Winner: MDF
Round 5: Moisture Resistance – A Clear Advantage for Treated Plywood
Moisture is the Achilles’ heel for standard MDF, while certain types of plywood are specifically engineered to withstand humid environments. This difference in moisture resistance is crucial when choosing materials for exterior applications, bathrooms, kitchens, or any area prone to moisture exposure.
Plywood’s Resilience:
- Treated Options: Marine plywood, pressure-treated plywood, and other moisture-resistant varieties are designed for exposure to moisture, making them suitable for exterior applications or areas with high humidity. These treated plywood options are impregnated with preservatives and sealants that protect them from moisture damage, rot, and decay.
MDF’s Vulnerability:
- Susceptible to Swelling: Standard MDF readily absorbs moisture, leading to swelling, warping, and structural degradation. This vulnerability limits its use in humid environments or exterior applications unless specifically treated for moisture resistance.
- Limited Moisture-Resistant Options: While moisture-resistant MDF varieties exist, they are not as readily available or as durable as treated plywood options. These moisture-resistant MDF options often come at a higher cost and may not offer the same level of protection as their plywood counterparts.
Winner: Plywood
The Final Verdict: Choosing the Right Material for Your Project
As with any epic showdown, there’s no single winner in the plywood vs MDF battle. The “best” material hinges entirely on your project’s specific requirements. By carefully considering the strengths and weaknesses of each material, you can confidently select the one that aligns with your project’s demands, budget, and desired outcome.
Choose Plywood When:
- Strength and durability are paramount. This includes structural applications like framing, subfloors, and sheathing, as well as heavy-duty furniture or projects requiring impact resistance.
- The project involves structural applications or load-bearing elements. Plywood’s superior strength makes it the ideal choice for applications where structural integrity and the ability to support weight are crucial.
- Moisture resistance is crucial, especially for exterior use or humid environments. Opt for treated plywood varieties like marine plywood or pressure-treated plywood for projects exposed to moisture, humidity, or the elements.
Choose MDF When:
- A smooth, consistent surface for painting or veneering is desired. This makes it ideal for cabinetry, furniture, moldings, and other projects where a flawless finish is paramount.
- Cost-effectiveness is a primary concern. MDF’s affordability makes it an attractive option for budget-conscious projects, especially those where material costs are a significant factor.
- The application doesn’t require exceptional strength or moisture resistance. Choose MDF for interior projects in dry environments where a smooth, paintable surface is prioritized over extreme strength or moisture resistance.
Table 1: Plywood vs MDF – A Quick Reference Guide
Feature | Plywood | MDF |
---|---|---|
Strength & Durability | High | Moderate |
Smoothness & Finish | Moderate | High |
Moisture Resistance | Varies (Treated options excel) | Low (Limited resistant options) |
Cost | Higher | Lower |
Ideal Applications | Structural framing, subfloors, sheathing, heavy-duty furniture, exterior applications (treated) | Cabinetry, furniture, molding & trim, signboards, interior applications |
Frequently Asked Questions: Plywood vs MDF
1. Can I use MDF for exterior projects?
While standard MDF is highly susceptible to moisture damage, there are moisture-resistant MDF varieties available. However, even these specialized options may not offer the same level of durability and longevity as treated plywood in exterior applications. For outdoor projects or areas exposed to humidity, treated plywood, like marine plywood, remains the superior choice.
2. Which material is easier to work with, plywood or MDF?
Both materials have their advantages and disadvantages when it comes to workability. Plywood is generally easier to cut and shape with standard woodworking tools, while MDF’s dense structure may require specialized saw blades to prevent chipping. However, MDF’s smooth surface requires less sanding and preparation for finishing, potentially saving time and labor costs.
3. Is plywood always more expensive than MDF?
Generally, yes. Plywood, especially higher grades or specialty types like marine plywood, tend to be more expensive than MDF due to the manufacturing process and the quality of the wood veneers used. However, the cost difference may vary depending on factors like wood species, thickness, and market conditions.
4. Can I paint or stain both plywood and MDF?
Yes, both materials can be painted or stained. However, MDF’s smooth, uniform surface provides a superior base for paint, resulting in a smoother, more professional-looking finish with less preparation. Plywood’s wood grain may require additional sanding or filling to achieve a perfectly smooth painted surface.
5. Which material is more environmentally friendly?
Both plywood and MDF can be considered sustainable building materials when sourced from responsibly managed forests. Plywood utilizes thin wood veneers, maximizing the use of harvested timber, while MDF utilizes wood fibers that might otherwise be considered waste. Look for products certified by organizations like the Forest Stewardship Council (FSC) to ensure responsible sourcing.