In the complex and often unpredictable world of logistics and shipping, ensuring the safe and damage-free transport of goods is not just a goal; it’s a business imperative. Every stage of the supply chain, from the factory floor to the end consumer’s doorstep, demands robust and reliable packaging solutions. When it comes to providing superior protection, structural integrity, and peace of mind, LVL slats for packing are emerging as a game-changer, setting a new standard for excellence in the industry.
What are LVL Slats and Why Should You Care?
LVL, short for Laminated Veneer Lumber, isn’t just another piece of wood; it’s an engineered marvel in the realm of building materials. This innovative product is created through a sophisticated manufacturing process that bonds thin sheets of wood veneer together under carefully controlled heat and pressure. The secret to its exceptional strength lies in the strategic arrangement of these veneer layers. The grain of each layer is alternated during the bonding process, resulting in a cross-grained structure that’s significantly stronger and more dimensionally stable than traditional solid wood.
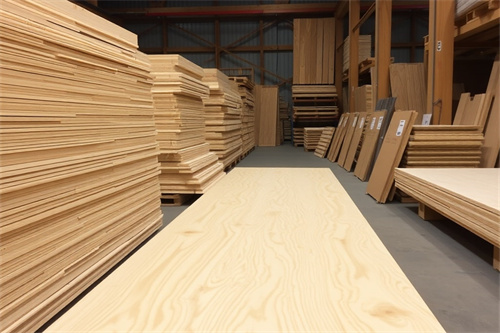
But why, you might ask, should you, a discerning business owner or logistics manager, care about the intricacies of LVL slats? The answer is simple: Enhanced protection, cost savings, and sustainability.
- Unmatched Strength and Durability: LVL slats possess an exceptional strength-to-weight ratio, meaning they can withstand heavy loads and resist the rigors of shipping, including impacts, vibrations, and changes in humidity. This inherent strength translates to less damage in transit, reducing the likelihood of costly product returns, replacements, and the accompanying logistical headaches.
- Cost-Effective Solution: While the initial cost of LVL might appear slightly higher than some traditional packing materials, it’s crucial to consider the long-term financial benefits. The superior durability and protective qualities of LVL slats minimize the risk of product damage during shipping, ultimately saving you money on replacements, returns, and potential damage claims.
- Sustainable Choice: In an era of increasing environmental awareness, choosing sustainable materials is no longer a mere marketing tactic; it’s a business imperative. LVL aligns perfectly with this demand for eco-friendly solutions. It’s typically manufactured using fast-growing, readily renewable wood species, promoting responsible forestry practices and minimizing the overall environmental impact.
How LVL Slats Elevate Your Packing Game
Imagine this: You’re tasked with shipping a large, fragile piece of equipment across the country, navigating a complex network of trucks, trains, and cargo ships. Traditional packing methods might involve bulky wooden crates or excessive amounts of plastic foam padding, adding significant weight and cost to your shipment while potentially falling short in terms of adequate protection.
Now, envision a smarter approach. Picture using precisely cut LVL slats strategically placed within the packaging to create a robust internal framework. This framework acts as a protective exoskeleton, absorbing shocks and vibrations during transit and distributing weight evenly to prevent damage to the valuable contents within.
Here’s a closer look at the tangible ways LVL slats elevate various aspects of the packing process:
- Enhanced Protection for Fragile Goods: Whether you’re shipping delicate electronics, fragile glassware, valuable artwork, or finely crafted furniture, LVL slats provide superior impact resistance and structural support. Their ability to absorb shocks and vibrations during transit minimizes the risk of damage, ensuring your products arrive at their destination in pristine condition.
- Increased Stacking Strength: For businesses dealing with heavier goods, optimizing storage and transportation space is crucial for efficiency and cost control. LVL slats, when incorporated into pallet designs, significantly increase their load capacity and stacking strength. This allows for higher and more secure stacking without compromising the integrity of the load, maximizing storage space and reducing transportation costs.
- Reduced Packaging Waste: The use of LVL slats often allows for a reduction in other packing materials, such as bulky wooden supports or excessive plastic padding. This not only contributes to cost savings but also aligns with your company’s sustainability goals by minimizing packaging waste and reducing your overall environmental footprint.
Comparing LVL Slats to Other Common Packing Materials
Choosing the right packing materials is a critical decision that directly impacts the safety of your products and the efficiency of your shipping operations. Let’s compare LVL slats to other commonly used packing materials to understand why they stand out as a superior choice:
Material | Strength | Durability | Cost | Sustainability |
---|---|---|---|---|
Solid Wood | High | Moderate | Low | Moderate |
Plywood | Moderate | Moderate | Low | Moderate |
Plastic (Expanded Polystyrene) | Low | Low | Low | Low |
Cardboard | Low | Low | Low | High |
LVL Slats | Very High | High | Moderate | High |
As the table clearly illustrates, LVL slats offer a compelling combination of exceptional strength, impressive durability, and commendable sustainability compared to other common packing materials. This unique blend of attributes makes them the ideal choice for businesses seeking to optimize their packing processes and enhance their commitment to environmental responsibility.
Practical Applications of LVL Slats in Packing
The versatility of LVL slats is truly remarkable, making them suitable for a wide range of packing applications across various industries. Here are some practical examples of how businesses are leveraging the strength and adaptability of LVL slats to enhance their packing operations:
- Crating: The Gold Standard for Secure Shipping: LVL slats are exceptionally well-suited for constructing strong, lightweight crates ideal for shipping large, heavy, or irregularly shaped items. Compared to traditional wooden crates, which can be bulky, prone to moisture damage, and often require additional reinforcement, LVL crates offer superior protection, reduced weight, and ease of assembly.
- Palletizing: Maximizing Efficiency in Storage and Transport: Pallets are the unsung heroes of the logistics world, facilitating the efficient movement of goods across the supply chain. By incorporating LVL slats into pallet designs, businesses can significantly enhance their load capacity, stacking strength, and overall durability. This translates to optimized storage space in warehouses, reduced transportation costs, and a lower risk of pallet failure during handling.
- Internal Bracing: Safeguarding Individual Items Within Bulk Shipments: When shipping multiple items within a larger container or crate, securing and protecting each item individually is crucial to prevent damage from shifting or impact during transit. LVL slats are often used to create robust internal bracing systems within packaging, acting as protective dividers or supports that keep individual items securely in place, minimizing the risk of damage.
- Custom Packaging Solutions: Tailored Protection for Unique Products: In today’s world of specialized products and intricate designs, one-size-fits-all packaging simply doesn’t cut it. The customizable nature of LVL allows for the creation of bespoke packaging solutions tailored to the specific dimensions, weight, and fragility of your products. This level of customization ensures optimal protection during transit, minimizes material waste, and reflects a commitment to quality that resonates with customers.
Making the Switch to LVL Slats: Factors to Consider
While the benefits of LVL slats for packing are undeniable, making the switch requires careful consideration of your specific needs and operational parameters. Here are some key factors to keep in mind as you evaluate the suitability of LVL slats for your packing operations:
- Product Dimensions and Weight: Before incorporating LVL slats into your packaging, it’s essential to assess the size, weight, and fragility of the goods you’re shipping. This information will determine the appropriate thickness, width, and spacing of the LVL slats required to provide adequate support and protection during transit.
- Shipping Distance and Conditions: The distance your shipments will travel and the potential hazards they might encounter along the way play a significant role in determining the level of protection needed. Consider factors such as the mode of transportation (truck, train, ship, air), the expected handling conditions (rough or gentle), and potential environmental factors (temperature fluctuations, humidity) to determine the optimal LVL slat configuration for your specific needs.
- Budget and Sustainability Goals: While LVL slats offer long-term cost savings through reduced damage and increased efficiency, it’s essential to consider your budget constraints and weigh them against the sustainability benefits of choosing a renewable material. Evaluate the initial cost of LVL slats compared to your existing packing materials and factor in the potential long-term savings associated with reduced damage, replacements, and waste disposal.
Conclusion: Pack Smarter, Ship Safer with LVL Slats
In the fiercely competitive and ever-evolving world of logistics and shipping, optimizing your packing processes is no longer a mere suggestion; it’s a strategic imperative for success. Protecting your products, controlling costs, minimizing your environmental impact, and exceeding customer expectations are all interconnected goals that can be achieved through informed decision-making and the adoption of innovative solutions.
LVL Slats for Packing: Your In-Depth Questions Answered
1. What makes LVL slats a superior choice for heavy-duty packing compared to plywood?
While both LVL and plywood are engineered wood products offering enhanced strength compared to solid wood, LVL slats stand out as the superior choice for heavy-duty packing. This advantage boils down to their unique construction. LVL is manufactured by layering thin wood veneers with their grain running in alternating directions, then bonding them under heat and pressure. This cross-grained structure creates consistent strength across the entire length of the slat, making it exceptionally resistant to bending and breaking under heavy loads. Plywood, on the other hand, typically features a cross-grained structure only in alternating layers, making it more susceptible to bending or warping under stress, especially over longer spans.
2. Can LVL slats be treated for moisture resistance, especially for overseas shipments?
Absolutely. Recognizing that moisture can compromise the integrity of even the strongest packing materials, manufacturers offer treatments to enhance the moisture resistance of LVL slats. These treatments can include specialized coatings or chemical impregnations that repel water and protect the wood from humidity. This is particularly crucial for overseas shipments where exposure to varying climates and prolonged periods at sea can create damp environments. By opting for treated LVL slats, you add an extra layer of protection for your goods, ensuring they remain safe and dry throughout their journey.
3. How do I determine the correct thickness and spacing of LVL slats for my specific products?
Determining the ideal thickness and spacing of LVL slats is not a one-size-fits-all approach; it requires a tailored assessment of your specific needs. Factors to consider include the weight, size, and fragility of your products. Heavier items naturally require thicker and more closely spaced slats for adequate support. Similarly, fragile items might benefit from closer slat spacing to minimize movement and potential damage during transit. The stacking height also plays a role, as higher stacks exert greater pressure on the lower levels, necessitating stronger support. For optimal design and safety, consulting with packaging engineers or experienced LVL suppliers is highly recommended. They can provide expert guidance based on your product specifications and shipping requirements.
4. Are there any specific regulations or standards I need to be aware of when using LVL slats for packing?
Yes, it’s crucial to be aware of and comply with relevant regulations and standards governing wood packaging materials. One prominent regulation is ISPM 15 (International Standards for Phytosanitary Measures), which aims to prevent the international spread of plant pests through wood packaging. ISPM 15 mandates specific treatments, such as heat treatment or fumigation, for wood packaging materials exceeding a certain thickness. These treatments ensure that the wood is free from harmful organisms that could potentially infest recipient countries. Always confirm with your LVL slat supplier that their products meet ISPM 15 requirements or other relevant regulations for your intended shipping destinations.
5. Can LVL slats be integrated with other packing materials for enhanced protection?
Absolutely! LVL slats are highly versatile and can be seamlessly integrated with other packing materials to create a comprehensive and robust protection system tailored to your specific product needs. For instance, combining LVL slats with corrugated cardboard boxes provides a strong outer shell while the slats offer internal reinforcement and weight distribution. Foam inserts can be added for cushioning delicate items, while molded pulp provides eco-friendly protection against shocks and vibrations. This flexibility allows you to customize your packing solutions for optimal protection, ensuring your products reach their destination in pristine condition.