Packing plywood, the unsung hero of countless industries, plays a crucial role in ensuring goods arrive safely and securely at their destination. This robust and versatile material provides a reliable surface for crating, bracing, and protecting valuable items during transit and storage. This comprehensive guide delves into the world of packing plywood, exploring its unique properties, diverse applications, advantages, and the key factors to consider when choosing the perfect sheet for your packing needs.
Unpacking the Essentials: What is Packing Plywood?
Packing plywood, also known as crating plywood or shipping plywood, is a specific type of plywood engineered for strength, durability, and cost-effectiveness in packing and shipping applications. While it shares similarities with other plywood types, packing plywood possesses distinct characteristics that set it apart.
Here’s a closer look at the key features that define packing plywood:
- Structural Integrity: Packing plywood is typically constructed with a focus on strength and stiffness to withstand the rigors of transportation and handling. It’s designed to resist bending, warping, and impact, ensuring the safe arrival of goods. This structural integrity is achieved by using strong adhesives and cross-graining the layers of veneer, distributing the load and enhancing its overall strength.
- Cost-Effective Materials: Unlike higher-grade plywood used for furniture or marine applications, packing plywood often utilizes less expensive wood species and may have cosmetic imperfections on the outer veneers. This focus on cost-effectiveness makes it an economical choice for packing applications where appearance is less critical. For instance, softwoods like pine and fir are commonly used in packing plywood due to their availability and affordability, while hardwoods like oak or maple, though stronger, are reserved for applications demanding higher strength and durability.
- Versatile Thicknesses: Packing plywood is available in a range of thicknesses to accommodate varying load requirements. Thinner sheets are suitable for lighter items, while thicker sheets provide the strength and rigidity needed for heavier or more delicate goods. The most common thicknesses range from 1/4 inch to 3/4 inch, with thicker sheets available for specialized heavy-duty applications.
- Surface Treatments: Depending on the intended application and environment, packing plywood may be treated with moisture-resistant coatings or finishes to enhance its durability and protect it from the elements during transit or storage. These treatments can include water-resistant coatings, anti-fungal agents, and insect repellents, ensuring the plywood withstands challenging environmental conditions during transportation or storage.
Beyond the Box: Exploring the Applications of Packing Plywood
Packing plywood’s versatility extends far beyond simple boxes. Its strength, affordability, and ease of use make it a valuable material for various packing and shipping solutions across numerous industries.
Here are some notable applications of packing plywood:
- Crating: Packing plywood serves as the primary material for constructing sturdy crates to protect heavy machinery, industrial equipment, and other bulky items during transportation. Its strength and rigidity ensure the crate can withstand the stresses of lifting, moving, and stacking.
- Target Users: Manufacturers, distributors, and logistics companies involved in shipping heavy or oversized items rely on packing plywood crates for their robust protection during transit.
- Advantages in Crating: Packing plywood’s ability to be cut to specific dimensions, its strength-to-weight ratio, and its affordability make it a practical choice for crating applications.
- Bracing and Blocking: Within crates and shipping containers, packing plywood is used to create internal bracing and blocking systems that secure items in place, preventing shifting and damage during transit. This is particularly important for fragile or delicate items that require extra protection.
- Target Users: Packing and shipping departments, moving companies, and anyone transporting fragile or delicate items benefit from packing plywood’s ability to create secure and customized bracing systems.
- Advantages in Bracing and Blocking: Packing plywood’s ease of cutting and shaping allows for the creation of custom bracing and blocking solutions tailored to the specific dimensions and fragility of the items being shipped.
- Palletizing: Packing plywood is often used as a top surface for pallets, providing a smooth and stable base for stacking and securing goods. This helps distribute weight evenly and prevents damage to items from the pallet structure itself.
- Target Users: Warehouses, distribution centers, and any industry utilizing pallets for storage or transportation benefit from the added strength and stability packing plywood provides.
- Advantages in Palletizing: Packing plywood creates a more robust and damage-resistant surface for palletized goods, reducing the risk of punctures, tears, or other damage during handling and transportation.
- Shipping Containers: Packing plywood can be used to line the interior walls and floors of shipping containers, providing an additional layer of protection against moisture, dirt, and impact. This is especially useful for goods sensitive to environmental conditions.
- Target Users: Exporters, importers, and anyone shipping goods internationally or over long distances often utilize packing plywood to enhance the protection offered by standard shipping containers.
- Advantages in Shipping Containers: Packing plywood lining helps regulate humidity levels within the container, protecting goods from moisture damage, especially during long sea voyages or exposure to varying climates.
- Custom Packaging Solutions: Packing plywood’s versatility allows for the creation of custom packing solutions tailored to specific items. This includes custom-sized boxes, inserts, and protective coverings designed to safeguard unique or irregularly shaped objects.
- Target Users: Specialized manufacturers, artists, and anyone shipping valuable, fragile, or uniquely shaped items benefit from custom packing solutions crafted from packing plywood.
- Advantages in Custom Packaging: Packing plywood’s workability allows for the creation of intricate designs and precise fits, ensuring optimal protection for delicate or irregularly shaped items that wouldn’t fit securely in standard packaging.
Weighing the Benefits: Advantages and Disadvantages of Packing Plywood
Like any material, packing plywood has its own set of advantages and disadvantages. Understanding these trade-offs is crucial for making informed decisions about its suitability for your packing needs.
Advantages | Disadvantages |
---|---|
Cost-Effective: Packing plywood is generally more affordable than higher-grade plywood options, making it a budget-friendly choice for packing and shipping applications where appearance is not paramount. This cost-effectiveness stems from the use of less expensive wood species and a greater tolerance for cosmetic imperfections, making it an economical choice for many packing needs. | Cosmetic Imperfections: Packing plywood often prioritizes functionality over aesthetics, so it may have cosmetic imperfections like knots, voids, or color variations on its surface. These imperfections do not affect its structural integrity but may not be suitable for applications where appearance is critical. For instance, if the packing plywood will be visible in a retail setting or used for display purposes, its appearance might be a concern. |
Strong and Durable: Offers a good balance of strength and durability to withstand the rigors of transportation and handling, ensuring the safe arrival of goods. Its cross-grained construction and strong adhesives provide resistance to impact, bending, and warping, making it suitable for protecting valuable items during transit. | Moisture Sensitivity: While some packing plywood may have moisture-resistant treatments, it’s generally not as moisture-resistant as marine plywood. Prolonged exposure to moisture or humid environments can lead to warping, swelling, or mold growth. Choose treated plywood or additional protective measures, such as plastic sheeting or desiccants, for such conditions. If the packing will be exposed to rain or high humidity, consider additional protective measures. |
Versatile and Easy to Work With: Can be easily cut, shaped, and assembled into various packing solutions, making it suitable for both simple and complex packing needs. Its workability makes it adaptable to various packing requirements, from basic crates to intricate custom packaging designs. | Weight Considerations: Depending on the thickness and wood species, packing plywood can add significant weight to shipments, potentially increasing shipping costs. Consider the weight of the plywood when calculating shipping expenses and explore lighter-weight alternatives if weight is a major concern. For instance, using corrugated cardboard inserts or lighter-weight wood species for internal bracing can help reduce overall weight. |
Widely Available: Packing plywood is readily available from lumberyards, building supply stores, and online retailers, making it easy to source for various packing projects. Its widespread availability makes it a convenient choice for businesses and individuals needing packing materials on short notice. | Environmental Impact: The production of plywood, including packing plywood, involves the use of wood resources and manufacturing processes that can have environmental impacts. Consider sourcing plywood from sustainably managed forests or exploring alternative packing materials made from recycled or renewable resources to minimize environmental impact. Look for certifications like the Forest Stewardship Council (FSC) logo, which indicates the wood comes from responsibly managed forests. |
Reusable and Recyclable: Packing plywood can often be reused for multiple shipments or repurposed for other applications, reducing waste and maximizing its value. Its durability allows for multiple uses, making it a more sustainable choice compared to single-use packing materials. |
Choosing Wisely: Factors to Consider When Selecting Packing Plywood
Selecting the right packing plywood involves considering several key factors to ensure you choose a material that meets your specific packing requirements and budget:
- Plywood Grade: While packing plywood doesn’t adhere to the same grading standards as other plywood types, it’s essential to consider the quality and appearance of the veneers. This is particularly important if the plywood will be visible or used in applications where aesthetics matter.
- “C” Grade (or lower): This grade typically signifies a lower quality veneer with visible imperfections like knots, knotholes, and color variations. It’s suitable for applications where appearance is not a primary concern, such as for internal bracing or hidden surfaces. For instance, if you’re building a crate where the interior surfaces won’t be visible, using “C” grade plywood can help reduce costs without compromising structural integrity.
- “D” Grade (or higher): This grade indicates a smoother veneer with fewer imperfections, making it more suitable for applications where appearance matters, such as for visible surfaces of crates or boxes. If you’re building a shipping box for a product that will be visible to the customer, using “D” grade plywood can enhance the overall presentation and create a more professional look.
- Wood Species: Different wood species offer varying levels of strength, weight, and cost-effectiveness. Choosing the right species depends on the specific requirements of your packing application.
- Softwoods (Pine, Fir): Generally more affordable and lightweight, suitable for lighter-duty applications or when weight is a concern. Softwoods are a cost-effective choice for many packing needs, especially when shipping costs are a major factor.
- Hardwoods (Oak, Maple): Offer greater strength and durability, making them suitable for heavy-duty packing or when added protection is required. Hardwoods are a more robust option for packing heavy machinery, industrial equipment, or items that require extra protection during transit.
- Thickness: The thickness of the plywood directly relates to its strength and load-bearing capacity. Selecting the appropriate thickness ensures the packing is strong enough to support the weight of the items being shipped and withstand the rigors of handling.
- Thinner Sheets (1/4″ – 3/8″): Suitable for lighter items or internal bracing within crates. These thinner sheets are cost-effective and provide adequate support for lighter loads.
- Thicker Sheets (1/2″ – 3/4″ or more): Necessary for heavier items, structural components of crates, or when increased rigidity is required. Thicker sheets offer greater load-bearing capacity and are essential for packing heavy or fragile items that require extra protection.
- Surface Treatments: Consider whether your packing application requires additional protection against moisture, insects, or other environmental factors. Choosing the right surface treatments ensures the packing plywood withstands the challenges of its intended environment.
- Moisture-Resistant Treatments: Look for plywood treated with water-resistant coatings or finishes if the packing will be exposed to moisture or humidity. These treatments help prevent warping, swelling, and mold growth, ensuring the packing remains intact and protects its contents.
- Insect-Resistant Treatments: Consider plywood treated with insecticides or pest-repellent finishes if the packing will be stored in areas prone to insect infestation. These treatments help deter insects from damaging the plywood and potentially infesting the goods being stored or shipped.
- Budget Considerations: Balance the level of protection required with your budget constraints. While higher-grade plywood and additional treatments offer enhanced performance, they also come at a higher cost. Carefully assess your packing needs and prioritize features that provide the necessary protection without exceeding your budget.
FAQs: Addressing Common Queries About Packing Plywood
1. What’s the difference between packing plywood and regular plywood?
While both are made from layers of wood veneer, packing plywood prioritizes strength and cost-effectiveness over appearance. It often uses less expensive wood species and may have cosmetic imperfections, making it ideal for packing applications where aesthetics aren’t paramount.
2. Can I use packing plywood outdoors for extended periods?
While packing plywood offers decent durability, prolonged outdoor exposure can lead to moisture damage. If you need plywood for outdoor applications, consider exterior-grade plywood with enhanced moisture resistance.
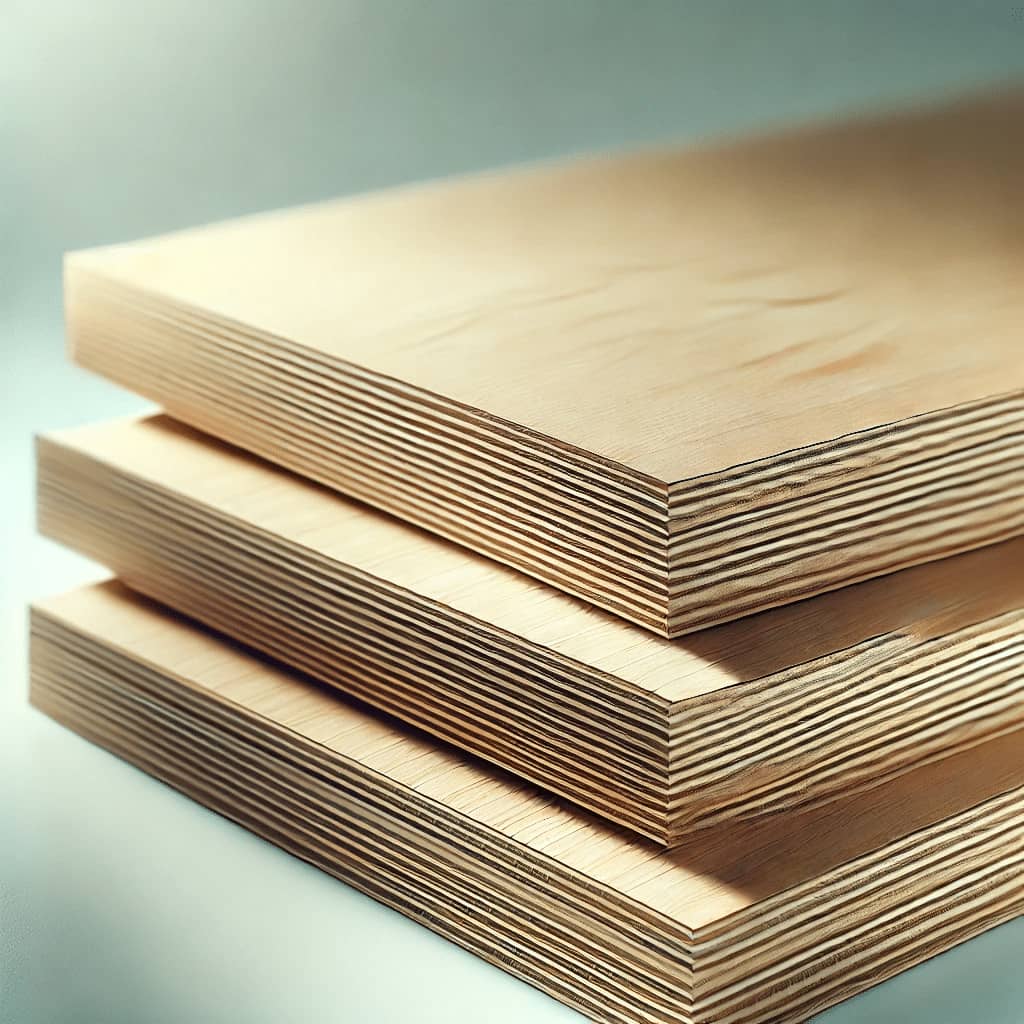
3. How do I determine the right thickness of packing plywood for my needs?
Consider the weight and fragility of the items being shipped. Heavier or more delicate items require thicker plywood for adequate support and protection. Consult a packing expert if you’re unsure about the appropriate thickness.
4. Can I reuse packing plywood for multiple shipments?
Yes, packing plywood’s durability often allows for reuse, especially if it hasn’t been structurally compromised. Inspect it for any damage before reusing it to ensure it still provides adequate protection.
5. Where can I purchase packing plywood?
Packing plywood is readily available at lumberyards, building supply stores, and some online retailers. When purchasing, inquire about wood species, thickness, and any available treatments to ensure you’re getting the right type for your packing needs.
Conclusion: Packing Plywood – A Reliable Choice for Secure Shipping
In the world of packing and shipping, where ensuring the safe and secure arrival of goods is paramount, packing plywood stands as a reliable and versatile solution. Its strength, affordability, and ease of use make it an indispensable material for protecting valuable items during transit and storage. By understanding its unique properties, diverse applications, and the key factors to consider when choosing the right sheet, you can confidently select the perfect packing plywood to meet your specific needs and ensure your goods arrive at their destination in pristine condition.