When it comes to conquering the unforgiving marine environment, only the toughest materials will do. Marine plywood, meticulously engineered to withstand the relentless assault of water, humidity, and harsh conditions, stands as the unsinkable choice for a diverse range of maritime applications. From the sleek hulls of sailboats to the sturdy foundations of oceanfront docks, this remarkable material forms the backbone of countless marine projects, offering a unique blend of strength, durability, and resilience that sets it apart from its landlocked counterparts.
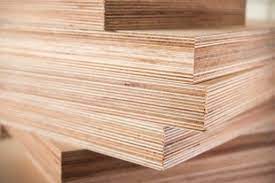
What Makes Marine Plywood Seaworthy?
Marine plywood isn’t simply regular plywood taking a casual dip in the ocean. It’s a meticulously crafted material, engineered from the inside out to thrive in demanding marine environments. Here’s a closer look at the key factors that contribute to its seaworthy reputation:
- Water-Resistant Core: Unlike standard plywood, which may use interior-grade glues susceptible to moisture damage, marine plywood boasts a core bonded with specialized marine-grade adhesives. These adhesives, often formulated with waterproof phenolic resins or similar compounds, are designed to create an impenetrable bond between the veneer layers. This prevents delamination, a common issue with standard plywood in moist environments, and ensures the plywood’s structural integrity even when exposed to prolonged moisture.
- Durable Hardwood Veneers: Marine plywood typically features hardwood veneers, such as Douglas fir, Okoume, Meranti, or Western Larch, chosen for their inherent strength, rot resistance, and ability to hold up against the rigors of marine environments. These veneers are carefully selected for their lack of defects, such as knots, voids, or resin pockets, which could compromise the plywood’s strength and durability in demanding marine applications. The use of high-quality hardwood veneers ensures that the plywood can withstand the stresses of marine environments without compromising its structural integrity.
- Void-Free Construction: One of the hallmarks of marine plywood is its void-free construction. Unlike standard plywood, which may contain small voids or gaps between veneer layers, marine plywood is manufactured to eliminate these potential weak points. This meticulous construction, often achieved through a combination of precise veneer layup and high-pressure bonding, ensures that the plywood remains structurally sound and resists water infiltration, even under extreme stress or impact. This void-free construction is crucial for preventing water from seeping into the plywood’s core, which could lead to rot, delamination, and structural failure over time.
- Superior Resistance to Moisture, Fungi, and Decay: Marine plywood undergoes rigorous treatments and coatings to enhance its resistance to the elements. Pressure treatments, where preservatives are forced deep into the wood fibers, provide long-lasting protection against fungal attack, decay, and marine borers, organisms that can wreak havoc on unprotected wood in marine environments. Additionally, specialized marine-grade coatings, often formulated with UV inhibitors and water repellents, create a moisture-resistant barrier on the plywood’s surface, further enhancing its durability and longevity in harsh marine environments.
Why Choose Marine Plywood: Navigating the Benefits
In the world of marine construction, where durability and longevity are paramount, marine plywood stands as a beacon of reliability. Let’s explore the key benefits that make it the preferred choice for discerning boat builders and maritime enthusiasts:
- Unwavering Strength and Stability: The cross-grained construction of marine plywood, where each veneer layer’s grain runs perpendicular to its adjacent layers, creates a panel that’s exceptionally strong and dimensionally stable. This inherent strength-to-weight ratio makes it ideal for constructing hulls, decks, and other structural components that need to withstand the stresses of wind, waves, and heavy loads, providing a robust yet lightweight solution for marine applications. The cross-grained construction distributes stress evenly across the panel, making it less likely to warp, bend, or break under pressure.
- Exceptional Resistance to Moisture Damage: Marine plywood’s use of waterproof adhesives and its void-free construction make it highly resistant to moisture damage. Unlike standard plywood, which can delaminate, swell, or rot when exposed to water, marine plywood maintains its structural integrity and resists warping, even in prolonged wet conditions, making it the ideal choice for boat hulls, decks, and other marine structures constantly exposed to moisture. This resistance to moisture damage translates into reduced maintenance requirements and a longer lifespan for marine structures, making it a cost-effective choice in the long run.
- Resilience Against Fungal Attack and Decay: The harsh marine environment is a breeding ground for fungi, bacteria, and other microorganisms that can wreak havoc on wood, leading to rot, decay, and structural weakening. Marine plywood’s treatment with preservatives and its use of naturally durable hardwood veneers provide exceptional resistance to these destructive forces, ensuring a longer lifespan and reduced maintenance requirements compared to less durable materials. This resistance to biological degradation is crucial for ensuring the safety and longevity of marine structures.
- Versatility in Marine Applications: From small boat building and repairs to large-scale dock construction and marine infrastructure, marine plywood’s versatility shines through. Its availability in various thicknesses, sizes, and finishes, coupled with its ability to be shaped and formed into complex curves and shapes, makes it adaptable to a wide range of marine projects, allowing builders and designers to bring their maritime visions to life with confidence. Whether you need to create curved hull sections, flat deck panels, or intricate interior components, marine plywood can be shaped and molded to meet the demands of the project.
- Sustainability for the Seas: Many marine plywood manufacturers are committed to sustainable forestry practices, sourcing their wood from responsibly managed forests that prioritize conservation and environmental responsibility. Choosing marine plywood from certified sustainable sources, such as those certified by the Forest Stewardship Council (FSC), allows you to build with a conscience, minimizing your impact on the marine ecosystems you cherish. By choosing sustainable marine plywood, you contribute to the long-term health of our forests and oceans.
Setting Sail with Applications: Exploring the Versatility of Marine Plywood
Marine plywood’s remarkable properties make it the material of choice for a vast array of maritime applications, serving the needs of boat builders, dock constructors, marine engineers, and water sports enthusiasts alike. Let’s dive into some of its most common and essential uses:
1. Boat Building and Repair:
- Target Users: Boat builders, both professional and amateur, shipyards, boat repair shops, and DIY enthusiasts undertaking boat building or restoration projects.
- Applications:
- Hulls: Marine plywood is a mainstay in boatbuilding, used to construct hulls for a wide range of vessels, from small dinghies, canoes, and sailboats to larger yachts, fishing boats, and even some commercial vessels. Its strength-to-weight ratio, formability, and resistance to water damage make it ideal for creating durable and seaworthy hulls.
- Decks: Marine plywood’s durability and water resistance make it the perfect material for constructing boat decks that can withstand constant exposure to the elements, foot traffic, and the rigors of marine environments.
- Bulkheads, Cabins, and Interior Components: Marine plywood’s versatility extends beyond structural components. It’s also used to create interior structures, cabins, berths, cabinetry, shelving, hatches, and other furniture within boats, providing a durable and aesthetically pleasing solution for boat interiors.
- Advantages: Its strength-to-weight ratio, moisture resistance, and ability to be shaped into complex curves make it a top choice for boat construction and repair, offering boat builders a reliable and versatile material to bring their designs to life.
2. Dock Construction and Marine Structures:
- Target Users: Marine contractors specializing in waterfront construction, dock builders, marina developers, and waterfront property owners.
- Applications:
- Piers and Docks: Marine plywood’s resistance to rot, decay, and marine borers makes it the ideal material for constructing durable and long-lasting piers and docks that can withstand the constant exposure to water, fluctuating tides, and the corrosive effects of saltwater environments.
- Walkways and Platforms: Its strength, stability, and resistance to moisture make it suitable for creating safe and reliable walkways, platforms, and access points in marine environments, providing stable surfaces for pedestrians and equipment.
- Jetties and Breakwaters: Marine plywood can be used in the construction of jetties, breakwaters, and other coastal protection structures, helping to safeguard coastlines from erosion, storm surges, and the damaging effects of wave action.
- Advantages: Its durability, resistance to the elements, and ability to withstand heavy loads make it essential for marine infrastructure projects, ensuring the longevity and safety of these critical structures.
3. Marine Furniture and Interiors:
- Target Users: Boat outfitters, marine interior designers, furniture makers specializing in marine-grade pieces, and DIY enthusiasts looking to outfit their boats or waterfront properties with durable and stylish furniture.
- Applications:
- Cabinets and Shelving: Marine plywood’s moisture resistance makes it ideal for creating durable and long-lasting cabinets, shelving units, and storage solutions for boats, waterfront homes, bathrooms, and other areas exposed to humidity.
- Tables and Seating: Its strength and stability make it suitable for constructing tables, benches, chairs, and other seating arrangements that can withstand the rigors of marine environments, providing comfortable and durable furniture for boats and outdoor spaces.
- Wall Paneling and Interior Trim: Marine plywood can be used to create attractive and durable wall paneling, wainscoting, ceiling liners, and interior trim for boats, boathouses, waterfront homes, and other areas where a nautical aesthetic is desired, adding warmth and character to interior spaces.
- Advantages: Its moisture resistance, durability, and aesthetic appeal make it a top choice for marine furniture and interiors, offering a combination of practicality and style for marine environments.
4. Other Notable Applications:
- Surfboard and Paddleboard Construction: Marine plywood’s lightweight yet strong nature, coupled with its ability to be shaped into curves, makes it suitable for crafting durable surfboards, paddleboards, and other water sports equipment that can withstand the impact of waves and the rigors of water sports.
- Kayak and Canoe Building: Its buoyancy, strength, and ability to be shaped make it a popular choice for kayak and canoe construction, providing a stable and reliable platform for these popular watercraft.
- Aquarium and Water Feature Construction: Marine plywood’s waterproof nature, resistance to rot, and ability to hold water make it suitable for building aquariums, ponds, water gardens, and other water features, providing a durable and long-lasting material for aquatic environments.
- Outdoor Signage and Displays in Coastal Environments: Its durability, resistance to the elements, and ability to withstand harsh coastal conditions make it a reliable choice for outdoor signage, billboards, and displays in coastal areas, ensuring that signs and displays remain intact and legible even in challenging weather conditions.
Choosing the Right Marine Plywood: Navigating the Grades and Options
Selecting the appropriate marine plywood for your project requires understanding the grading system and the various treatment options available, ensuring you choose a material that meets the specific demands of your marine application.
Grading System:
Marine plywood is typically graded based on its face veneer quality and the number of allowable defects, which influences its appearance, workability, and suitability for different applications.
Grade | Description | Typical Applications |
---|---|---|
A | Highest grade with smooth, paintable face veneers and minimal defects, such as knots or color variations. | Boat interiors, cabinetry, high-end furniture, applications where a pristine finish is desired. |
B | Allows for slightly more surface imperfections than Grade A, such as small knots or slight color variations. | Boat exteriors, decks, structural components, applications where appearance is less critical but durability remains important. |
C | May have some knots, plugs, and other cosmetic imperfections that don’t affect its structural integrity. | Utility applications, subflooring, hidden structural components, applications where appearance is not a primary concern. |
Treatment Options:
Understanding the various treatment options available allows you to further tailor the marine plywood to your specific needs, enhancing its resistance to various environmental factors.
- Pressure-Treated: Infused with preservatives under pressure to enhance resistance to rot, decay, and insects. Ideal for applications in contact with water or ground, such as dock pilings, fence posts, or sill plates.
- Tropical Hardwood Veneers: Some marine plywood utilizes tropical hardwoods like Okoume, known for their natural durability, rot resistance, and dimensional stability in humid environments. These hardwoods often possess natural oils and resins that provide inherent protection against moisture and pests.
- Epoxy Coating: Applying a marine-grade epoxy coating to all surfaces of the plywood provides an additional layer of moisture protection and enhances its durability. Epoxy coatings create a hard, waterproof barrier that resists abrasion, UV degradation, and chemical exposure, making the plywood even more resistant to the harsh marine environment.
Why Choose Yuantuo Wood for Your Marine Plywood Needs?
You understand the critical role marine plywood plays in your maritime projects. You need a supplier who understands those needs just as deeply, providing not just a product, but a partnership built on quality, reliability, and a shared passion for conquering the marine environment. That’s where Yuantuo Wood sets sail above the rest.
Here’s why discerning builders and maritime enthusiasts choose Yuantuo Wood:
- Uncompromising Quality: We source only the finest marine-grade hardwoods and utilize state-of-the-art manufacturing techniques to ensure our plywood consistently meets the highest standards of strength, durability, and water resistance.
- Tailored to Your Needs: We offer a wide range of marine plywood options, from different hardwood species to various thicknesses, grades, and treatments, allowing you to select the perfect material for your specific project requirements.
- Sustainability at Our Core: We believe in protecting the very environments our products are designed to withstand. That’s why we prioritize sourcing our wood from responsibly managed forests, ensuring a sustainable future for the maritime industry.
- Experienced Guidance: Our team of experts possesses deep knowledge of marine plywood applications. We’re here to provide guidance, answer your questions, and help you choose the right materials to ensure the success of your project.
- Reliability You Can Trust: We understand that timelines and project deadlines are crucial in the marine industry. That’s why we’re committed to delivering on time, every time, with consistent quality and exceptional customer service.
When you choose Yuantuo Wood, you’re not just choosing marine plywood; you’re choosing a partner dedicated to your success on the water.
Marine Plywood FAQs: Your Questions Answered
1. What is the lifespan of marine plywood in a marine environment?
While the lifespan of marine plywood can vary depending on factors like exposure to the elements, maintenance, and quality of construction, it’s known for its longevity. With proper care and maintenance, marine plywood structures can last for decades.
2. Can I use regular plywood for marine applications?
Using regular plywood for marine applications is strongly discouraged. Regular plywood lacks the water-resistant adhesives, durable veneers, and protective treatments found in marine plywood, making it highly susceptible to moisture damage, rot, and delamination in marine environments.
3. How do I protect marine plywood from UV damage?
Prolonged exposure to UV radiation can degrade the surface of marine plywood over time. To protect it, apply a marine-grade paint or varnish containing UV inhibitors, which will create a protective barrier against the sun’s harmful rays.
4. What type of fasteners should I use with marine plywood?
When working with marine plywood, it’s crucial to use fasteners specifically designed for marine environments, such as stainless steel screws or bronze nails. These materials resist corrosion caused by saltwater and moisture, ensuring the longevity of your construction.
5. Can I paint or varnish marine plywood?
Yes, marine plywood can be painted or varnished to enhance its appearance and provide additional protection from the elements. Be sure to use marine-grade paints and varnishes specifically formulated for use in marine environments, as they offer superior moisture resistance, UV protection, and durability.