In the dynamic world of construction, where innovation meets precision, concrete reigns supreme as the building material of choice. But behind every awe-inspiring concrete structure, from towering skyscrapers to elegant bridges, lies a hidden hero, silently shaping and supporting these architectural marvels: formwork plywood.
Formwork plywood, also known as shuttering plywood, is a specialized construction panel engineered to create temporary molds, or forms, that hold and shape wet concrete as it cures. But this is no ordinary plywood. It’s a testament to engineering ingenuity, designed to withstand the demanding conditions of a construction site while ensuring flawless concrete finishes. Think of it as the unsung hero holding its breath underwater, patiently waiting for the concrete to harden into the desired shape. Without formwork plywood, achieving the structural integrity and smooth, refined surfaces characteristic of modern concrete structures would be a herculean task.
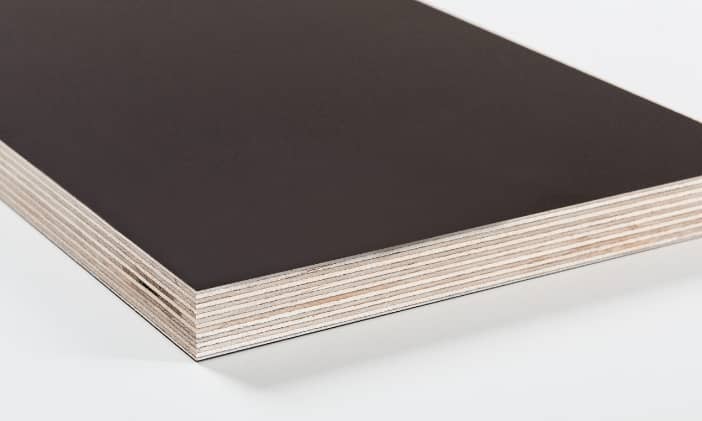
Why Formwork Plywood Matters: The Backbone of Concrete Construction
Formwork plywood is the unsung hero of concrete construction, playing a critical role in determining the success and aesthetic appeal of any project involving concrete. It’s the silent workhorse that ensures your vision translates into a tangible, durable reality.
Here’s why formwork plywood is indispensable:
- Strength and Stability: Imagine the immense pressure exerted by tons of wet concrete, a force akin to a giant’s handshake. Formwork plywood stands strong, resisting this pressure to prevent bowing, deflection, and potential structural failures. It’s the reliable backbone that ensures your concrete structures are built to last, from foundations to high-rise walls.
- Smooth Concrete Surfaces: The quality of your concrete finish is a direct reflection of the formwork used. Formwork plywood, with its smooth, uniform surface, ensures a pristine finish, minimizing the need for extensive (and expensive!) post-pour finishing work. This translates to significant cost savings and a faster construction process, allowing you to deliver projects on time and within budget.
- Reusability: In an era of increasing environmental awareness, reusability is key. Formwork plywood is designed to withstand multiple concrete pours, acting like a reusable mold for your concrete creations. This makes it a sustainable choice that reduces material waste and lowers the overall environmental footprint of your projects, aligning with the growing demand for eco-conscious construction practices.
Formwork Plywood vs. Standard Plywood: A Tale of Two Materials
The construction industry offers a plethora of materials, and it’s tempting to opt for cheaper alternatives. However, when it comes to concrete formwork, using standard plywood is like bringing a knife to a gunfight. It simply can’t compete with the specialized performance of formwork plywood.
Let’s break down the key differences:
Feature | Formwork Plywood | Standard Plywood |
---|---|---|
Strength & Durability | Engineered for extreme pressure and multiple uses, ensuring long-term reliability and cost-effectiveness. Think of it as the seasoned marathon runner of the plywood world. | Designed for general purposes, making it susceptible to damage and warping under the weight and moisture of concrete. Imagine a sprinter attempting a marathon – not a pretty sight. |
Moisture Resistance | Impregnated with special resins and often featuring sealed edges, providing exceptional resistance to moisture damage and ensuring a longer lifespan. It laughs in the face of moisture. | Lacks the specialized treatments of formwork plywood, making it highly susceptible to water damage, swelling, and delamination, compromising the concrete finish and structural integrity. Water is its kryptonite. |
Surface Smoothness | Features high-quality face veneers that result in a smooth, uniform concrete finish, minimizing the need for extensive finishing work. It’s like having a built-in smoothing tool for your concrete. | Often has a rougher surface that can transfer imperfections to the concrete, requiring additional labor and cost for smoothing and finishing. Prepare for a bumpy ride and extra work. |
Reusability | Can withstand 20+ concrete pours, making it a cost-effective and sustainable choice for multiple projects. It’s the gift that keeps on giving. | Typically lasts for only 1-2 pours before needing replacement, increasing material waste and project costs. One-hit-wonder, unfortunately. |
Cost | Higher initial investment, but its exceptional durability and reusability result in significant long-term cost savings. Think of it as an investment that pays dividends over time. | Lower initial cost, but its shorter lifespan and susceptibility to damage lead to higher replacement and labor costs in the long run. Penny wise, pound foolish? |
Long-Term Value | A wise investment that pays dividends in terms of durability, reusability, and superior concrete finishes. The reliable workhorse that delivers exceptional value over time. | A risky choice that can lead to costly repairs, delays, and compromised concrete quality. A gamble that might leave you with more headaches than rewards. |
The Verdict: While standard plywood might seem appealing initially, its limitations become glaringly apparent in demanding concrete applications. Formwork plywood, with its superior performance and longevity, is the clear winner, ensuring project success and maximizing your investment.
Delving Deeper: The Anatomy of Formwork Plywood
Understanding the key components of formwork plywood provides valuable insights into its exceptional performance and empowers you to make informed decisions when selecting the right material for your construction needs.
- Hardwood Veneers: Formwork plywood is typically constructed with hardwood veneers, such as birch, poplar, or eucalyptus, chosen for their inherent strength, density, and smooth surface. These veneers are cross-grained and bonded together with strong adhesives, creating a panel that resists warping, cracking, and delamination, even under the immense pressure of wet concrete. It’s like a tightly woven fabric of strength and resilience.
- Resin Impregnation: Moisture is the nemesis of any wood product. That’s why formwork plywood undergoes a special treatment: impregnation with moisture-resistant resins, typically phenolic or melamine. These resins penetrate deep into the wood fibers, creating a formidable barrier against water damage and ensuring the plywood maintains its structural integrity throughout multiple uses. It’s like giving the plywood a suit of armor against the elements.
- Edge Sealing: The edges of a plywood panel are its most vulnerable points, where moisture can easily seep in. Formwork plywood addresses this vulnerability through edge sealing, where a waterproof sealant is applied to the edges, providing an additional layer of protection against moisture ingress and further extending the lifespan of the plywood. It’s like sealing the deal on moisture resistance.
- Surface Films (Optional): For projects demanding the smoothest concrete finishes or enhanced durability, film-faced formwork plywood is the gold standard. These panels feature a durable plastic film overlay on their face, providing exceptional moisture resistance, abrasion resistance, and a glass-like finish to the concrete, minimizing the need for post-pour finishing work and enhancing the aesthetic appeal of the final product. It’s like giving your concrete a flawless complexion.
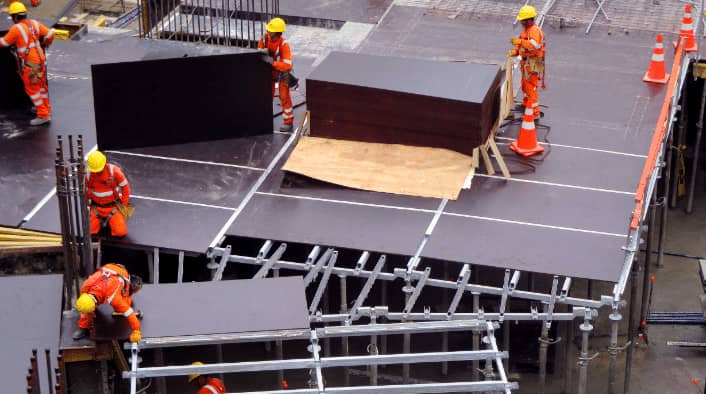
Factors Influencing Formwork Plywood Selection: A Builder’s Checklist
Choosing the right formwork plywood is crucial for optimizing your construction process and ensuring the longevity of your structures. Here’s a checklist to guide your selection:
- Project Scale and Budget: Every project has unique demands. Larger projects with higher concrete pours, such as high-rise buildings or large infrastructure projects, require thicker, higher-grade plywood to withstand the increased loads and ensure multiple uses. Smaller projects, such as residential foundations or retaining walls, might benefit from thinner, more economical options without compromising quality. It’s about finding the right tool for the job.
- Concrete Design Complexity: Intricate architectural designs with curves or unique shapes, such as curved walls or arches, necessitate thinner, more flexible plywood that can be easily molded to achieve the desired forms. Simpler designs, on the other hand, can utilize standard thicknesses without sacrificing structural integrity. It’s about matching the plywood’s flexibility to the design’s complexity.
- Reusability Requirements: Sustainability is no longer optional. If maximizing reusability is a priority, investing in higher-grade, film-faced plywood is a wise decision. It significantly extends the lifespan of the plywood, reduces material waste, and lowers long-term costs, contributing to a more environmentally responsible construction process. It’s about building for the future, not just for today.
- Environmental Considerations: In today’s world, every industry must do its part to protect the environment. Choosing plywood made from sustainably sourced wood, certified by organizations like the Forest Stewardship Council (FSC), and compliant with low formaldehyde emission standards is a testament to your commitment to responsible construction practices and a healthier built environment. It’s about building a better world, one structure at a time.
Beyond the Basics: Exploring Specialized Formwork Plywood
The world of construction is constantly evolving, and formwork plywood has evolved alongside it, leading to the development of specialized types designed to meet specific construction needs:
- Oversized Formwork Plywood: For large-scale infrastructure projects or structures with massive concrete pours, such as dams, bridges, or tunnels, oversized formwork plywood panels are indispensable. These massive panels, often exceeding standard sizes, reduce the number of joints required, creating a more seamless and structurally sound concrete surface, essential for projects where strength and continuity are paramount.
- Curved Formwork Plywood: Architects and designers often envision curved concrete elements, such as arches, tunnels, or curved walls, to add aesthetic appeal and structural complexity to their designs. Achieving these curved forms requires specialized flexible formwork plywood that can be bent to the desired radius without compromising strength or stability, ensuring a flawless finish and structural integrity. It’s like bending the rules of concrete construction without breaking them.
- Textured Formwork Plywood: Concrete doesn’t have to be purely functional; it can also be aesthetically versatile. Textured formwork plywood allows you to add visual interest to your concrete surfaces. These panels feature embossed patterns that are imprinted onto the concrete during curing, creating unique textures and designs that enhance the aesthetic appeal of your structures, from subtle patterns to bold designs.
Why Choose Yuantuo Wood for Your Formwork Plywood Needs?
You’ve just delved into the crucial role formwork plywood plays in creating stunning, durable concrete structures. Now, let’s explore why Yuantuo Wood should be your trusted partner in bringing those structures to life.
- Uncompromising Strength and Durability: At Yuantuo Wood, we understand that your projects demand nothing less than the best. Our formwork plywood is crafted from premium hardwood veneers, meticulously selected and expertly engineered to withstand the immense pressures and demanding conditions of concrete construction. We prioritize strength and durability, ensuring your projects stand the test of time.
- Flawless Finishes, Every Time: We believe that beautiful concrete starts with exceptional formwork. Our commitment to smooth, uniform surfaces in our plywood translates to pristine concrete finishes, minimizing costly and time-consuming rework. Choose Yuantuo Wood and achieve the high-quality aesthetics your projects deserve.
- Sustainability at Our Core: Yuantuo Wood is dedicated to responsible forestry practices and minimizing our environmental impact. Our commitment to sourcing sustainable wood and utilizing eco-friendly production processes aligns with your goals for greener construction.
- Global Reach, Local Expertise: With a presence in over 40 countries, Yuantuo Wood brings extensive experience and a deep understanding of diverse construction needs. We’re your reliable partner, wherever your projects take you.
Partner with Yuantuo Wood and experience the difference that quality formwork plywood makes in your concrete construction projects. We’re dedicated to providing the superior materials and unwavering support you need to build beyond expectations.
FAQs: Addressing Your Formwork Plywood Queries
1. How does the resin impregnation in formwork plywood benefit concrete finishes?
The resin impregnation isn’t just about making the plywood water-resistant; it also plays a crucial role in achieving those smooth, flawless concrete surfaces. The resin helps prevent the concrete’s moisture from penetrating the plywood, reducing the likelihood of grain transfer and surface imperfections. This means less time and money spent on post-pour finishing work.
2. My project has a tight budget. Are there situations where using standard plywood for formwork might be acceptable?
While we always recommend formwork plywood for its superior performance, using standard plywood might be acceptable for very small-scale, non-critical applications with only one or two concrete pours planned. However, this should be carefully assessed, considering potential risks and the higher long-term costs associated with its shorter lifespan.
3. Can I use textured formwork plywood to create exposed concrete walls with a specific design?
Absolutely! Textured formwork plywood is an excellent choice for achieving unique aesthetic effects on exposed concrete surfaces. By choosing panels with the desired pattern, you can imprint that design directly onto the concrete, eliminating the need for additional surface treatments or finishes.
4. What are some tips for maximizing the lifespan of my formwork plywood?
Proper care and handling can significantly extend the lifespan of your investment. This includes:
- Thorough Cleaning: Remove all concrete debris after each use to prevent moisture buildup and surface damage.
- Proper Storage: Store panels flat in a dry, well-ventilated area to prevent warping.
- Careful Handling: Avoid dropping or dragging panels, as this can lead to chipping and delamination.
- Timely Repairs: Address any minor damage promptly to prevent further deterioration.
5. Beyond the standard and specialized types, are there any emerging trends in formwork plywood technology?
The industry is continuously evolving. Some emerging trends include:
- Lightweight Formwork Plywood: These panels offer the same strength and durability but with reduced weight, improving handling and potentially reducing transportation costs.
- Bio-based Resins: Research is ongoing to develop formwork plywood using bio-based resins derived from renewable resources, further enhancing its sustainability profile.