In the symphony of construction, where strength and precision harmonize to create architectural marvels, concrete stands as the unwavering maestro. But behind every flawlessly cast concrete structure, working diligently behind the scenes, lies a silent guardian, shaping and supporting the symphony’s grand design: shuttering plywood.
Far more than just temporary formwork, shuttering plywood is a specialized building material meticulously engineered to withstand the demanding conditions of a construction site while ensuring impeccable concrete finishes. With a myriad of plywood options available, understanding the key shuttering plywood specifications & properties is paramount for selecting the perfect material to orchestrate your project’s success.
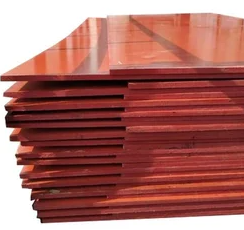
Why Shuttering Plywood Matters: A Cut Above the Rest
While standard plywood might appear as a budget-friendly option, its limitations become glaringly apparent when subjected to the rigors of concrete formwork. Shuttering plywood, on the other hand, is purpose-built to conquer these challenges, boasting a unique symphony of characteristics that set it apart:
- Exceptional Strength and Durability: Crafted to withstand heavy concrete loads, endure repeated use, and resist the wear and tear of harsh site conditions, ensuring consistent performance and a longer lifespan, ultimately saving time and resources.
- Unwavering Moisture Resistance: Impregnated with specialized resins and protective coatings, shuttering plywood effectively repels water absorption, preventing warping, swelling, and delamination that can compromise the structural integrity of the concrete and lead to costly repairs.
- Flawless Concrete Finishes: Featuring high-quality face veneers, shuttering plywood minimizes grain transfer, resulting in sleek, uniform concrete surfaces that require minimal finishing work, reducing labor costs and enhancing the aesthetic appeal of the final product.
- Champion of Reusability: Designed to withstand multiple concrete pours, shuttering plywood promotes sustainability by reducing material waste, lowering overall project costs, and minimizing the environmental impact of construction activities.
Shuttering Plywood vs. Standard Plywood: A Head-to-Head Comparison
Feature | Shuttering Plywood | Standard Plywood |
---|---|---|
Strength & Durability | High | Moderate |
Moisture Resistance | Excellent | Poor |
Surface Smoothness | Very Smooth | Relatively Rough |
Reusability | High (20+ pours) | Low (1-2 pours) |
Cost | Higher Initial Cost | Lower Initial Cost |
Long-Term Value | Excellent | Poor |
The Verdict: While standard plywood might offer a lower upfront cost, its lack of durability, moisture resistance, and reusability makes it a risky and potentially more expensive choice in the long run. Shuttering plywood, with its superior performance and longevity, proves to be a wise investment for any concrete construction project.

Decoding the Specs: Key Shuttering Plywood Properties
Navigating the world of shuttering plywood specifications can feel like deciphering an ancient language, but understanding these key properties will empower you to make informed decisions for your construction projects:
1. Wood Species and Plywood Grade:
- Hardwood Veneers: Typically sourced from hardwoods like birch, poplar, or eucalyptus, renowned for their exceptional strength, density, and naturally smooth surface, providing a solid foundation for concrete formwork.
- Plywood Grade: Specifies the quality and appearance of the face and back veneers, with higher grades indicating fewer imperfections, a smoother finish, and enhanced durability, directly impacting the final concrete surface quality.
2. Thickness and Size:
- Thickness: Ranges from 9mm to 21mm or more, with thicker sheets offering greater load-bearing capacity for larger concrete pours, deeper structural elements, and increased reusability.
- Size: Commonly available in 4′ x 8′ sheets, but custom sizes can be ordered to minimize waste, optimize material usage, and accommodate unique project requirements, reducing cutting and labor costs.
3. Moisture Resistance:
- Resin Impregnation: Shuttering plywood is typically impregnated with phenolic or melamine resins, penetrating deep into the wood fibers to enhance its moisture resistance, prevent water damage, and ensure long-lasting performance in demanding environments.
- Edge Sealing: The edges of the plywood, being particularly vulnerable to moisture ingress, are often sealed with a waterproof sealant, creating an additional barrier against moisture and further extending its lifespan.
4. Surface Film:
- Film-Faced Plywood: Some shuttering plywood comes with a durable plastic film overlay on its face, providing enhanced moisture resistance, exceptional abrasion resistance, and an ultra-smooth concrete finish, minimizing the need for post-pour finishing work.
5. Strength and Bending Properties:
- Modulus of Rupture (MOR): A crucial measure of the plywood’s resistance to bending and breaking under load, with higher values indicating greater strength and ability to withstand the pressure of wet concrete without deformation.
- Modulus of Elasticity (MOE): Indicates the plywood’s stiffness and its ability to resist deflection under pressure, ensuring that the formwork maintains its shape and the concrete cures evenly for optimal structural integrity.
6. Formaldehyde Emission Standards:
- CARB Phase 2 Compliant: Prioritizing worker health and indoor air quality is essential. Look for plywood that meets or exceeds California Air Resources Board (CARB) Phase 2 standards for low formaldehyde emissions, ensuring a safer and healthier working environment.
Shuttering Plywood Applications: Where Performance Meets Versatility
Shuttering plywood’s unique blend of strength, durability, and reusability makes it the go-to choice for a wide range of concrete construction applications:
Target Audience:
- Concrete Contractors: The backbone of concrete construction, relying on shuttering plywood’s reliability and performance for a wide range of projects.
- Formwork Specialists: Experts in creating complex concrete structures, leveraging shuttering plywood’s versatility and strength for demanding designs.
- Residential Builders: Utilizing shuttering plywood for foundations, walls, slabs, and other concrete elements in residential construction.
- Commercial Developers: Relying on shuttering plywood’s durability and reusability for large-scale commercial projects, from high-rises to infrastructure.
Major Applications:
- Foundations: Providing a strong and stable base for buildings and structures.
- Walls: Creating vertical concrete elements for both structural and aesthetic purposes.
- Slabs: Forming horizontal concrete surfaces like floors, roofs, and bridge decks.
- Columns and Beams: Constructing vertical and horizontal supports for load-bearing structures.
- Tunnels and Bridges: Forming complex curved structures for infrastructure projects.
Advantages in Specific Fields:
- High-Rise Construction: Shuttering plywood’s strength and reusability are essential for the repetitive concrete pours in high-rise buildings.
- Infrastructure Projects: Its durability and ability to withstand heavy loads make it ideal for bridges, tunnels, and other critical infrastructure.
- Architectural Concrete: The smooth finish and versatility of shuttering plywood allow for intricate designs and aesthetically pleasing concrete surfaces.
Making the Right Choice: Factors to Consider
Selecting the optimal shuttering plywood for your project involves carefully considering several factors to ensure a harmonious balance between performance, budget, and sustainability:
- Project Scale and Budget: Larger projects with higher concrete pours might require thicker, higher-grade plywood to withstand the increased loads and ensure multiple uses, while smaller projects might utilize thinner, more economical options.
- Concrete Design Complexity: Intricate designs with curves or unique shapes might necessitate thinner, more flexible plywood that can be easily molded to achieve the desired forms, while simpler designs can utilize standard thicknesses.
- Reusability Requirements: If maximizing reusability is a priority, investing in higher-grade, film-faced plywood can significantly extend its lifespan, reduce material waste, and lower long-term costs.
- Environmental Considerations: Choosing plywood made from sustainably sourced wood and compliant with low formaldehyde emission standards promotes responsible construction practices and a healthier built environment.
Shuttering Plywood Properties at a Glance: A Quick Reference Guide
Property | Description | Importance |
---|---|---|
Wood Species | Hardwood veneers (birch, poplar, eucalyptus) | Strength, durability, smooth surface |
Thickness | 9mm to 21mm or more | Load-bearing capacity |
Moisture Resistance | Resin impregnation, edge sealing | Prevents warping, swelling, and delamination |
Surface Film | Film-faced plywood (optional) | Enhanced moisture resistance, abrasion resistance, smooth finish |
Strength | Modulus of Rupture (MOR) | Resistance to bending and breaking |
Stiffness | Modulus of Elasticity (MOE) | Resistance to deflection |
Formaldehyde Emissions | CARB Phase 2 compliant | Improved indoor air quality |
Why Choose Yuantuo Wood for Your Bed Slat Needs?
Just as shuttering plywood provides the crucial support system for robust concrete structures, Yuantuo Wood bed slats form the often-unseen foundation for a comfortable and restful night’s sleep. Since 2014, we’ve been dedicated to crafting high-quality wooden bed slats that stand the test of time, mirroring the durability and reliability of shuttering plywood in the construction world.
Here’s how our commitment to quality aligns with the key principles of shuttering plywood:
- Built to Withstand the Test of Time: Just like shuttering plywood endures the rigors of a construction site, our bed slats are built to withstand years of nightly weight and movement. We use premium hardwoods chosen for their strength, resilience, and resistance to warping or breakage, ensuring a lasting foundation for your customers’ sleep.
- Smooth, Consistent Support: A smooth, uniform surface is crucial for both flawless concrete finishes and a comfortable sleeping experience. Our bed slats are carefully crafted to provide even, consistent support across the entire mattress surface, minimizing pressure points and maximizing comfort.
- Sustainable Sourcing for a Better Tomorrow: As the construction industry embraces eco-friendly materials like FSC-certified shuttering plywood, we share that commitment to sustainability. We source our wood from responsibly managed forests, ensuring the long-term health of our planet while delivering exceptional products.
- Strategically Located for Global Reach: Our factory’s proximity to Tianjin Port, mirroring the global reach of shuttering plywood standards, allows us to efficiently deliver our bed slats to clients worldwide, partnering with furniture makers across continents to provide superior sleep support.
Partner with Yuantuo Wood and build a foundation of quality, comfort, and sustainability for your customers. Contact us today to discuss your bed slat needs.
Shuttering Plywood FAQs: Delving Deeper into the Details
1. How many times can shuttering plywood be reused, and what factors influence its lifespan?
While shuttering plywood is designed for multiple uses, its actual lifespan hinges on a combination of factors:
- Plywood Quality: Higher-grade plywood, with its denser core, stronger adhesives, and more durable surface coatings, will inherently withstand more concrete pours compared to lower-grade options.
- Handling and Maintenance: Careful handling during installation and dismantling, thorough cleaning after each use, and proper storage are essential for preserving the plywood’s integrity and maximizing its reusability.
- Site Conditions: Exposure to extreme temperatures, prolonged moisture, harsh chemicals, and rough handling can all take a toll on the plywood’s condition, reducing its lifespan.
With proper care, high-quality, film-faced shuttering plywood can endure 20 or more concrete pours, while lower-grade plywood might only last for a few uses.
2. What are the advantages of using film-faced shuttering plywood, and are there any drawbacks?
Film-faced shuttering plywood offers a trio of compelling advantages:
- Enhanced Moisture Resistance: The film acts as a barrier against water absorption, preventing warping, swelling, and delamination, which are common issues with unprotected plywood.
- Increased Abrasion Resistance: The durable film overlay protects the plywood’s surface from scratches, scrapes, and impacts during installation, stripping, and concrete placement, extending its lifespan.
- Smoother Concrete Finish: The smooth film surface imparts a polished look to the concrete, minimizing the need for extensive post-pour finishing work, saving time and labor costs.
However, film-faced plywood typically comes at a higher initial cost compared to uncoated plywood. However, the long-term benefits of increased durability, reusability, and improved concrete finish often outweigh the initial price difference.
3. What is the difference between phenolic and melamine resin impregnation, and which one is better?
Both phenolic and melamine resins enhance plywood’s moisture resistance, but they possess distinct characteristics:
- Phenolic Resin: A more economical option, phenolic resin effectively repels water but may darken the wood’s color over time. It’s suitable for applications where aesthetics are less critical.
- Melamine Resin: Offering superior moisture resistance and color stability, melamine resin retains the wood’s natural appearance, making it ideal for projects demanding high-quality finishes.
The choice between phenolic and melamine resin depends on the specific project requirements and budget constraints.
4. Can shuttering plywood be used for curved concrete structures, and what factors should be considered?
Yes, shuttering plywood can be used to create curved concrete structures, but certain factors are crucial:
- Plywood Thickness: Thinner plywood, typically 9mm to 12mm, offers greater flexibility and is easier to bend into curved shapes without cracking or breaking.
- Bending Radius: Each plywood type has a specific bending radius, which determines the smallest curve it can achieve without compromising its structural integrity.
- Supporting Structure: Adequate support is essential for maintaining the desired curve during concrete placement. This might involve using closely spaced formwork ribs, flexible backing materials, or specialized curved formwork systems.
5. How should shuttering plywood be stored to maximize its lifespan, and what common mistakes should be avoided?
Proper storage is paramount for preserving shuttering plywood’s quality and extending its service life:
Best Practices:
- Store Flat: Always store plywood sheets flat on a level surface, supported evenly with blocks or timbers to prevent sagging, warping, and stress on the plywood’s structure.
- Dry and Ventilated Space: Choose a storage location that is dry, well-ventilated, and protected from rain, snow, direct sunlight, and extreme temperature fluctuations.
- Elevated Storage: Keep the plywood off the ground using pallets or blocks to allow for air circulation beneath the sheets, preventing moisture absorption from the ground.
Common Mistakes to Avoid:
- Leaning Plywood: Avoid leaning plywood sheets against walls or other surfaces, as this can lead to warping and bowing over time, compromising their flatness.
- Direct Ground Contact: Never store plywood directly on the ground, as moisture can seep in from below, causing swelling, delamination, and mold growth.
- Exposure to Elements: Protect plywood from direct sunlight, rain, and snow, as these elements can cause warping, discoloration, and deterioration of the wood and its protective coatings.