The maritime world demands materials that can weather the storm, literally. Enter boat building plywood, a stalwart of marine construction, prized for its strength, resilience, and ability to navigate the challenges of a life at sea. This in-depth exploration delves into the remarkable versatility of boat building plywood, revealing its crucial role in crafting everything from sleek sailboats to robust workboats.
Setting Sail with Strength: What Makes Boat Building Plywood Unique?
Boat building plywood isn’t your average construction material. It’s engineered from the ground up to withstand the punishing demands of marine environments. Here’s what sets it apart:
- Marine-Grade Core: Unlike standard plywood, which often uses softwood cores known for their affordability and ease of working, boat building plywood relies on durable hardwoods like Okoume, Meranti, or Douglas Fir. These species, often sourced from sustainably managed forests, are chosen for their exceptional rot resistance, decay resistance, and ability to withstand prolonged exposure to moisture without compromising structural integrity.
- Void-Free Construction: Every sheet of boat building plywood is crafted with a void-free core, meaning no gaps or air pockets exist between the layers. This meticulous construction ensures consistent strength across the entire panel, prevents water infiltration that could lead to rot or delamination, and provides a stable, reliable foundation for bonding with adhesives and applying finishes.
- Cross-Grained Layers: The secret to boat building plywood’s remarkable dimensional stability lies in its cross-grained construction. Each layer of wood veneer is laid perpendicular to the one below it, a technique that enhances strength by distributing stress evenly, prevents warping and twisting that can occur with changes in temperature and humidity, and ensures the panel holds its shape even under the demanding conditions encountered at sea.
- Water-Resistant Adhesives: Holding it all together are specialized marine-grade adhesives, typically classified as WBP (Water Boil Proof) or MR (Moisture Resistant). These adhesives, often formulated with low VOC content to minimize environmental impact, form a tenacious bond that resists delamination – the separation of plywood layers – and ensures the plywood remains structurally sound even with prolonged exposure to moisture, salt spray, and the harsh UV radiation experienced in marine environments.
Deconstructing the Construction: A Closer Look at Boat Building Plywood
Feature | Description |
---|---|
Type | Marine Plywood |
Core Material | Okoume, Meranti, Douglas Fir, Gaboon – chosen for their rot resistance, strength, and stability in humid environments. |
Veneer Species | Typically the same species as the core to ensure consistent performance, but can vary for specific applications, such as using a more durable species for the outer veneers. |
Adhesive | WBP (Water Boil Proof) or MR (Moisture Resistant) – specially formulated for marine environments to resist delamination and maintain bond strength. |
Typical Thickness | 4mm – 25mm (and thicker for specific structural applications) – thickness is chosen based on the structural requirements of the application. |
Standard Sheet Sizes | 4′ x 8′, 5′ x 10′, but custom sizes are often available to minimize waste and suit specific project needs. |
Grades | A-Grade (premium, smooth, ideal for visible surfaces), B-Grade (allows minor imperfections, suitable for painting or covering), C-Grade (structural, may have knots, used for hidden components) |
Standards | BS 1088 (British Standard), EN 314 (European Standard) – these standards ensure consistent quality and performance. |
Table 1: A Glimpse Inside Boat Building Plywood
Beyond the Hull: 7 Remarkable Applications of Boat Building Plywood
While often associated with hull construction, boat building plywood’s versatility extends far beyond this primary application. Here are seven notable examples, highlighting the diverse users and advantages of this remarkable material:
- Hull Construction: The backbone of countless vessels, boat building plywood’s exceptional strength-to-weight ratio makes it ideal for crafting hulls of various sizes and designs. From nimble sailboats slicing through the waves to robust motor yachts navigating open waters, boat building plywood provides a strong, reliable foundation. Its ability to be shaped into complex curves makes it suitable for both traditional and modern hull designs.
- Suitable for: Boat builders specializing in sailboats, motor yachts, fishing boats, and small craft.
- Advantages: High strength-to-weight ratio, ability to be shaped into complex curves, resistance to impact and water damage.
- Decking and Superstructures: Boat building plywood’s durability and unwavering resistance to moisture, UV radiation, and foot traffic make it a top choice for decking, cabin tops, and other superstructure elements exposed to the elements. Its ability to withstand the rigors of the marine environment ensures these critical components maintain their integrity and appearance over time.
- Suitable for: Boat builders, marine contractors, and DIY enthusiasts working on boat renovations and upgrades.
- Advantages: Durability, moisture resistance, UV resistance, ability to withstand foot traffic and impact.
- Interior Joinery: Stepping inside a well-crafted vessel, you’ll often find boat building plywood at the heart of its interior beauty and functionality. From elegant cabin interiors with warm wood tones to functional storage compartments designed for efficiency and durability, boat building plywood’s smooth surface, ability to hold finishes beautifully, and resistance to moisture make it ideal for crafting interior components that enhance both aesthetics and practicality.
- Suitable for: Boat interior specialists, carpenters, and joiners crafting high-quality marine interiors.
- Advantages: Smooth surface for finishing, ability to hold screws and fasteners well, resistance to moisture and humidity, creates a warm and inviting aesthetic.
- Bulkheads and Partitions: Safety and compartmentalization are paramount in marine construction. Boat building plywood’s structural integrity, sound-dampening properties, and fire-retardant qualities (when treated with specialized coatings) make it suitable for creating bulkheads and partitions that enhance safety, reduce noise transmission between compartments, and provide fire resistance in the event of an emergency.
- Suitable for: Boat builders, marine engineers, and contractors focused on safety and regulatory compliance.
- Advantages: Structural integrity, fire-retardant properties (when treated), sound-dampening qualities, ability to create watertight compartments.
- Furniture and Fittings: Boat furniture and fittings demand a unique blend of style, durability, and resistance to the rigors of marine use. Boat building plywood’s versatility extends to crafting durable and stylish furniture, cabinetry, and fittings that can withstand the constant motion, humidity, and occasional spills encountered at sea. Its ability to be shaped, finished, and customized allows for the creation of unique and functional pieces that enhance the onboard experience.
- Suitable for: Boat furniture makers, carpenters, and DIY enthusiasts seeking durable and stylish marine furniture.
- Advantages: Strength, moisture resistance, ability to be shaped and finished to create custom pieces, holds screws and fasteners securely.
- Transoms and Stringers: Beneath the sleek lines of a boat lie critical structural components responsible for transferring loads, providing support, and ensuring the vessel’s structural integrity. Transoms, the vertical structural members at the stern, and stringers, the longitudinal supports running the length of the hull, benefit from boat building plywood’s exceptional strength, resistance to flexing, and ability to withstand the constant stress of water pressure and impact.
- Suitable for: Boat builders and marine engineers designing and constructing structurally sound vessels.
- Advantages: High strength, resistance to flexing and fatigue, ability to withstand high-stress applications, ensures long-term structural integrity.
- Repair and Restoration: Time, weather, and the occasional mishap can take a toll on even the sturdiest vessels. Boat building plywood proves invaluable for repairing damaged hulls, decks, or structural components, restoring vessels to their former glory. Its compatibility with marine adhesives and finishes ensures a seamless and durable repair that maintains the structural integrity and aesthetics of the boat.
- Suitable for: Boat repair yards, restoration specialists, and DIY boat owners.
- Advantages: Easy to work with, compatible with marine adhesives and finishes, allows for strong and durable repairs, cost-effective solution for restoring damaged components.
Weighing the Options: Comparing Boat Building Plywood Suppliers
Supplier | Location | Price Range (per 4’x8′ sheet) | Specialties |
---|---|---|---|
Chesapeake Plywood | East Coast USA | $80 – $200 | Wide range of marine plywood species and grades, including FSC-certified options. Offers custom cutting services. |
Boulter Plywood | West Coast USA | $90 – $220 | Specializes in Okoume and Meranti plywood, known for their exceptional rot resistance and stability. Provides technical support and guidance on plywood selection. |
Yuantuo Wood | China | £60 – £180 | Offers a wide selection of FSC-certified marine plywood, prioritizing sustainable sourcing. Provides delivery throughout the UK and Europe. |
James Latham | UK & Ireland | £70 – £200 | Large distributor of timber and panel products, including a comprehensive range of marine plywood grades and species. Offers next-day delivery service. |
Atlantic Plywood | East Coast USA | $75 – $190 | Specializes in marine-grade plywood and lumber, offering a variety of species and thicknesses. Provides expert advice and support for boat building projects. |
Table 2: A Snapshot of Boat Building Plywood Suppliers
Navigating the Trade-offs: Advantages and Limitations of Boat Building Plywood
Advantages | Limitations |
---|---|
High Strength-to-Weight Ratio: Offers excellent strength without excessive weight, crucial for optimizing a boat’s performance and fuel efficiency. | Can be more expensive than standard plywood due to the use of higher-quality materials and specialized manufacturing processes. |
Excellent Moisture Resistance: Engineered to withstand prolonged exposure to water, humidity, and the harsh conditions encountered in marine environments. | Requires proper sealing and finishing to maintain longevity and prevent moisture infiltration that can lead to rot or delamination. |
Dimensional Stability: Resists warping, twisting, and cupping even in humid environments, ensuring the structural integrity and aesthetic appeal of boat components. | Susceptible to rot and decay if not properly protected from prolonged exposure to moisture or if left unfinished. |
Versatile and Easy to Work With: Can be cut, shaped, and fastened using standard woodworking techniques, making it accessible to both professional boat builders and DIY enthusiasts. | Can be heavy to handle, especially in larger sheet sizes, requiring proper lifting techniques and equipment. |
Table 3: Balancing the Pros and Cons of Boat Building Plywood
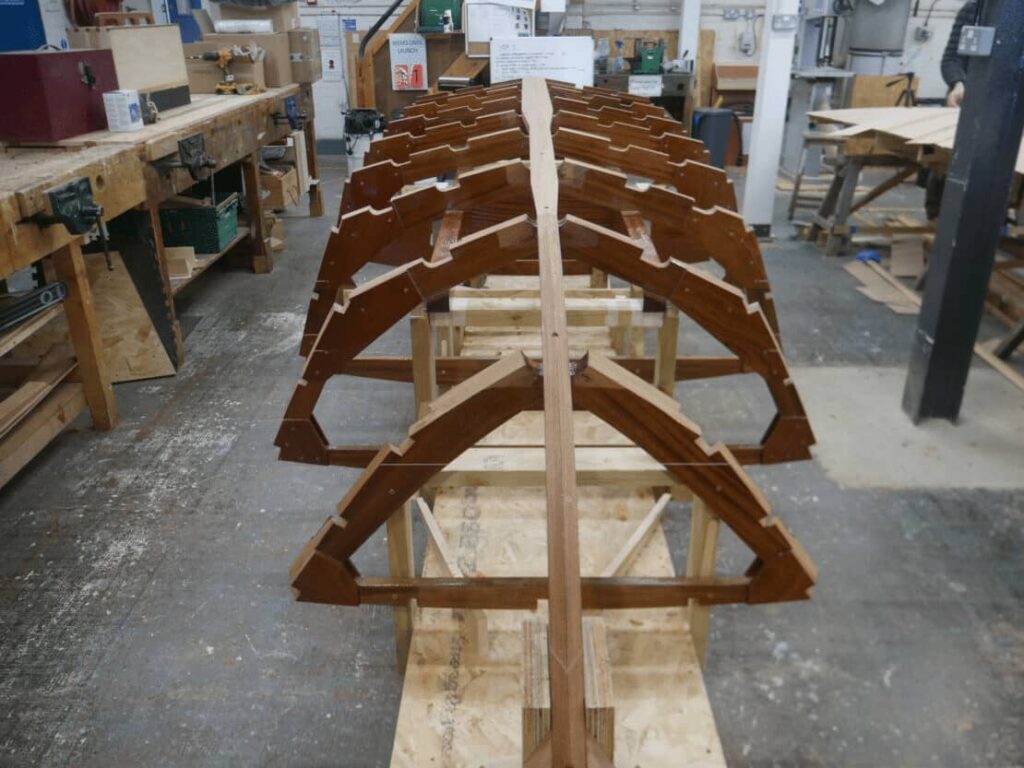
Diving Deeper: Exploring Related Aspects of Marine Plywood
- FSC Certification: For environmentally conscious builders, choosing FSC-certified boat building plywood ensures the wood is sourced from responsibly managed forests that prioritize environmental conservation, social responsibility, and economic viability.
- Epoxy Saturation: Saturating boat building plywood with epoxy resin enhances its water resistance, strength, and durability, making it even more resilient to the marine environment. This process involves completely sealing the wood pores with epoxy, creating a barrier against moisture, rot, and marine borers.
- CNC Machining: Computer Numerical Control (CNC) machining allows for precise cutting and shaping of boat building plywood, enabling intricate designs and complex components that would be challenging or impossible to achieve with traditional woodworking methods. This technology enhances precision, reduces waste, and opens up new possibilities in boat design and construction.
Answering Your Questions: FAQs About Boat Building Plywood
1. What is the typical lifespan of boat building plywood in a marine environment?
With proper maintenance, including regular inspections, meticulous sealing, and diligent application of protective finishes, boat building plywood can last for several decades in demanding marine environments. The key to longevity lies in preventing moisture infiltration, UV damage, and protecting the wood from marine borers.
2. Can I use standard plywood for boat building to reduce costs?
While tempting for its lower cost, using standard plywood for boat building is strongly discouraged. Standard plywood lacks the specialized marine-grade core, water-resistant adhesives, and void-free construction essential for withstanding the rigors of the marine environment. Using it for marine applications can lead to premature deterioration, structural issues, safety concerns, and ultimately, a shorter lifespan for your vessel.
3. What type of finish is best suited for protecting boat building plywood?
Epoxy-based paints and varnishes are popular and highly effective choices for finishing boat building plywood. They offer excellent water resistance, create a durable barrier against UV damage, and provide a long-lasting protective layer that resists abrasion, impact, and the harsh conditions encountered at sea.
4. How do I approach repairing minor damage to boat building plywood, such as scratches or gouges?
Small scratches or gouges can often be repaired using epoxy filler, a two-part compound that cures to a hard, durable finish that can be sanded and painted. For more significant damage, a patch of boat building plywood can be epoxied over the affected area, ensuring a strong and watertight repair.
5. Where can I source high-quality boat building plywood and receive expert advice on selecting the right materials for my project?
Reputable marine supply stores, lumberyards specializing in hardwoods, and online retailers specializing in boat building materials are excellent starting points. Look for suppliers who can provide detailed information about the plywood’s species, grade, adhesive type, and any certifications, such as FSC certification. Don’t hesitate to ask questions and seek guidance on selecting the most suitable plywood for your specific project requirements.
Related Blogs:
Boatbuilding Plywood Manufacturers: Delivering Unmatched Quality